Retraduzindo o Sistema Toyota de Produção – Parte 4: Redução de mão de obra e Qualidade
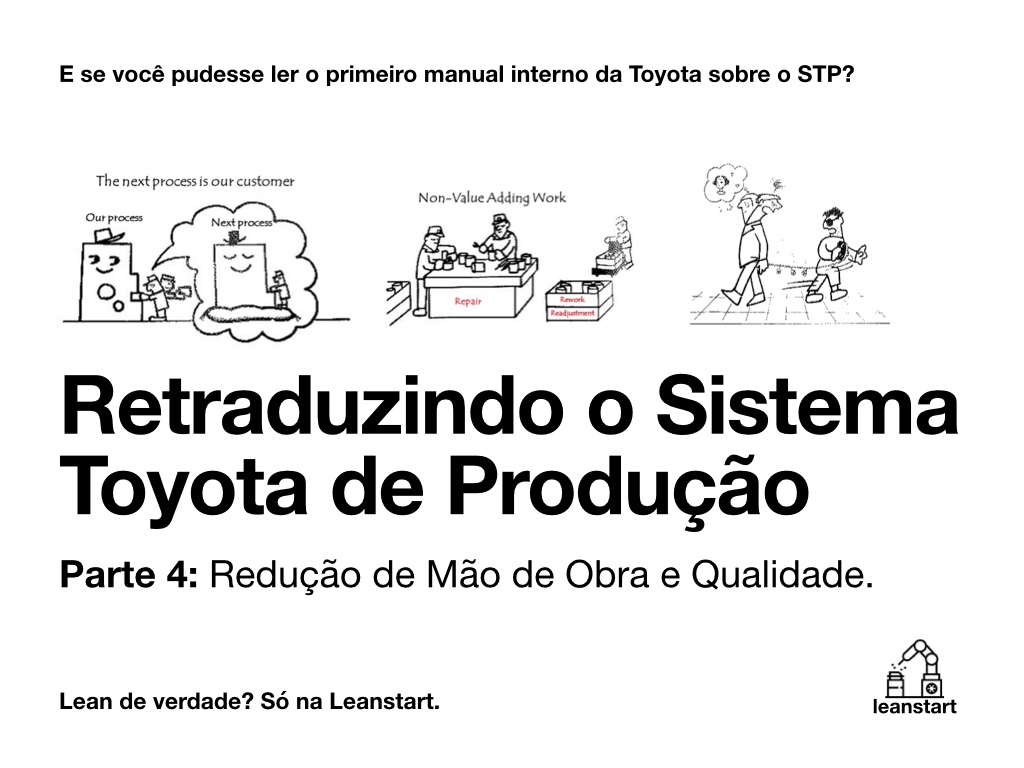
Sabia que a Toyota já dispensou passar por um processo de certificação ISO 9000? Ela fez uma análise e identificou que o Sistema Toyota de Produção, com suas profundas raízes e se comprometimento inegociável com a prática da Gestão da Qualidade Total (TQM) atendia e ainda superava alguns dos requisitos para a certificação. Conseguir o certificado não agregaria valor e seria somente mais um custo.
Em outras plantas, fora do Japão, ela teve que se certificar, mas porque a legislação do país e políticas internas de fornecedores e clientes exigiam o “diploma” na parede para fechar contratos.
Em quanto isso, nós nos orgulhamos do certificado na parede, que simplesmente significa que fazemos (ou que convencemos o auditor de que fazemos) nossa obrigação, aquilo que é o mínimo para conseguir manter um negócio aberto.
O que você está prestes a ver agora, na tradução da Seção 3 do Capítulo 1 do primeiro manual interno da Toyota sobre o STP, é simplesmente o que significa falar menos de qualidade, parar de acreditar que é diferencial, e fazer de forma pragmática, o que realmente tem que ser feito.
Seção 3: Redução de mão de obra e Qualidade
Sobre Qualidade
Nesta seção, explicaremos como se deve pensar sobre qualidade em relação às rotinas de redução de mão de obra, bem como qual a relação entre atividades de garantia de qualidade e redução de mão de obra.
A Qualidade é Construída dentro do Processo Produtivo
Estamos envolvidos na indústria automotiva e é nossa missão fornecer um carro sem problemas ao cliente. Para isso, é necessário fabricar produtos que atendam aos requisitos de qualidade do projeto, e isso impulsiona a necessidade de verificações de qualidade. Convencionalmente, os produtos acabados são verificados por um inspetor de qualidade e depois enviados para o seguinte processo de produção; não importa o quanto você avalie a qualidade de um produto que já foi fabricado, isso nunca levará à fabricação de produtos de boa qualidade.

Se o inspetor de qualidade executar uma inspeção de amostragem e declarar que os produtos são bons, mas um deles for considerado defeituoso, se nos colocarmos no lugar de nossos clientes, não há como dizer: “Não podemos fazer nada, é apenas um em mil. “
Todos os produtos são submetidos a uma inspeção de cem por cento, de uma forma ou de outra. Foi aí que nasceu a eliminação de inspetores dedicados de qualidade em tempo integral e o conceito de “construa a qualidade no processo de produção”. O que significa garantir completamente a qualidade em cada etapa do processo, onde ele só pode enviar um bom produto para o processo a seguir. A inspeção deve ser feita dentro do processo e os produtos defeituosos removidos no local.
Pelo conceito de “construir qualidade no processo de produção”, cada pessoa é responsabilizada. A ideia básica é que “o processo a seguir é nosso cliente”, não enviar um produto com defeito para o processo a seguir é a base da construção da qualidade no processo de produção.
Apesar desses esforços, algumas vezes um defeito será descoberto no processo a seguir. Se isso acontecer, eles entrarão em contato imediatamente com o processo anterior e o departamento interromperá o processo de produção, a causa raiz será investigada e as contramedidas implementadas.
Sem resposta imediata, os produtos defeituosos continuarão sendo produzidos. Além disso, é necessário que o processo que os produziu faça o retrabalho do produto com defeito. Ficar em silêncio só porque é uma falha menor nunca deve acontecer.
Permitir que o processo a seguir faça o retrabalho sem notificar o processo anterior é inaceitável. Isso pode resultar na produção de mais produtos defeituosos. O retrabalho deve ser feito pelo departamento que produziu o produto com defeito.
Qualidade é o Verdadeiro Valor da Melhoria
Construir produtos de boa qualidade é uma prioridade mais do que qualquer outra coisa para a nossa indústria de transformação. Não importa quantos produtos você produz, se forem de baixa qualidade, os clientes não os comprarão. Mesmo se você reduzir os custos de produção, se não puder vendê-los, haverá uma perda.
No caso de automóveis, a segurança é especialmente importante. Fracassaríamos em nossa responsabilidade social se trouxéssemos produtos para o mercado em que “escolhemos atalhos” ou apresentássemos a desculpa de “estávamos muito ocupados” ou “fizemos com que custasse menos”. Isso pode ser fatal para uma empresa.
Em resumo, garantir a qualidade é a primeira coisa que deve ser considerada. Você está priorizando uma coisa menos importante quando faz pouco disso por outras razões. Considere a que tipo de trabalho o termo “trabalho de garantia de qualidade” se refere.
Diferentemente do passado, quando a intuição do operador ou o grau de habilidade desempenhavam um papel maior, hoje cada processo é segmentado e é necessária menos especialização de habilidades. O trabalho padrão para cada processo de produção faz parte da garantia de qualidade.
O trabalho padronizado deve ser projetado para garantir a qualidade exigida. Se houver desigualdade entre os processos, o processo de verificação por observação visual ou medidor deve ser incorporado ao trabalho padrão como um único processo.
Se os defeitos ainda forem produzidos nessas condições, é porque o trabalho padronizado não é seguido ou porque há algum defeito em máquinas, equipamentos, moldes ou ferramentas. Entenda por que as pessoas não estão seguindo o trabalho padronizado.
Às vezes, as pessoas dizem coisas como: “Quando tentamos reduzir o trabalho, os defeitos aumentaram” ou “Reduzimos muitas pessoas, o que afetou a qualidade do produto”.
Como explicamos anteriormente, olhando para o conceito do STP, isso é colocar o carro à frente dos bois e nunca deve acontecer.
Observando que tipo de problemas ocorrem, eles podem ser amplamente divididos em duas categorias:
(A) Omitir ou esquecer alguns dos procedimentos necessários, com a impressão de que o trabalho deve ser concluído em um tempo menor. Em vez de eliminar atividades desnecessárias, elas acabam pegando atalhos.
(B) Como anteriormente tínhamos excedente de tempo alocado; era possível criar estoque intermediário e retrabalho. As reduções de mão de obra expuseram nossos defeitos de qualidade.
O caso de (A) é comumente encontrado em trabalhos de montagem realizados em linhas de montagem móvel. Esse erro ocorre porque a linha não foi parada para evitar atrasos no processo de produção.
Nas atividades de redução de mão de obra, as pessoas são bem ensinadas sobre a importância de interromper a linha. A primeira coisa a ensinar uma nova pessoa é como parar a linha.
Ao interromper a linha, podemos descobrir o desequilíbrio entre a quantidade de trabalho atribuída a cada pessoa e descobrir fatos para a eliminação de atividades desnecessárias. Também é possível resolver a causa fundamental do atraso.
Se as pessoas omitem algum trabalho porque não há tempo suficiente alocado, pode ser porque elas acham que a linha nunca deve ser interrompida. O supervisor é responsável por garantir que as pessoas entendam que a passagem de um produto completo para o processo a seguir é mais importante, mesmo que seja necessário interromper a linha.
Não há necessidade de ficar obcecado com a velocidade da linha ou o tempo de Takt. É importante esclarecer que “o tempo de Takt e o número de pessoas não têm relação”. A pessoa está fazendo tudo o que é necessário no seu próprio ritmo, para que um ciclo de trabalho seja concluído.
Se eles não terminarem dentro do tempo de Takt, a linha poderá ser parada até que seja concluída. Garantir que o trabalho se encaixe dentro do tempo necessário exige medidas completamente diferentes, e esse é o trabalho de gerentes, supervisores e técnicos.
Por exemplo, se uma pessoa precisar de 70 segundos para concluir do processo 1 ao processo 5 , enquanto o takt for 60 segundos, eles excederão o takt em 10 segundos. Não deve haver necessidade de explicar que nunca devemos omitir esses 10 segundos. As pessoas devem fazer seu trabalho normalmente e a linha deve parar por 10 segundos a cada vez para produzir produtos de boa qualidade.
O trabalho dos supervisores e técnicos é implementar melhorias para garantir que qualquer pessoa possa concluir os processos dentro de 60 segundos, trabalhando em ritmo normal. Ao reduzir atividades desnecessárias ou reduzir a distância que percorrem, com melhorias, não haveria necessidade de parar (atrasar) a linha.
Se você tentar eliminar a parada da linha sem melhorar o processo de trabalho, isso naturalmente resultará em uma menor qualidade dos produtos; isso deve ser rigorosamente evitado.
No caso (B), ao reduzir o número de pessoas e o estoque, vemos que muitos defeitos foram produzidos com frequência. Eles foram retrabalhados dentro do processo de produção, em vez de resolver a causa raiz.
Um processo a seguir corrige o defeito causado por um processo anterior sem fornecer feedback. Por exemplo, há uma incompatibilidade com o furo roscado devido a um problema de design. Você o corrige com os orifícios corretos dos parafusos no seu processo.
Como o problema é gerenciado, a causa raiz permanece sem solução. A mão de obra e o estoque adicionais para esses reparos improvisados aumentam o custo. Quando esses problemas se tornam óbvios por causa do processo de redução de mão de obra, é uma chance de melhorar.
Supervisores e técnicos devem devolver os produtos defeituosos aos seus respectivos departamentos. Eles devem visitar o processo anterior para buscar as causas raiz desses defeitos e resolvê-los, começando com a compreensão da causa raiz.
Isso pode ser comparado ao uso de analgésicos para apendicite crônica; em vez disso, você decide fazer uma cirurgia e se recuperar totalmente.
Esse conceito também se aplica à solução dos defeitos causados por máquinas, equipamentos, moldes e gabaritos, que descrevemos anteriormente. Se acharmos que o equipamento está causando um defeito, é importante interromper a linha imediatamente para identificar e eliminar a causa raiz.
Se acabarmos fazendo reajustes no processo por conta própria, apenas porque o departamento de manutenção não responde depois que entrarmos em contato com eles, poderemos começar a corrigir o problema em nosso próprio processo de produção, e isso imperceptivelmente se tornará parte do processo regular.
Não devemos parar com uma única solicitação por escrito ou uma única ligação. Devemos continuar a tomar medidas pacientemente até obtermos um produto de perfeita qualidade.
Defeitos e Inspeção
Pense por que o envio de um produto com defeito é inaceitável. Se a linha de montagem, que é o processo final de produção, envia produtos defeituosos, é altamente provável que um produto defeituoso chegue ao cliente.
Isso é inaceitável, porque isso afeta a confiabilidade da empresa e a credibilidade do produto, mais do que qualquer outra coisa. Normalmente, os defeitos são descobertos por inspeção e retrabalhados antes de serem vendidos ao cliente. Quanto mais a empresa está decidida a não colocar um produto defeituoso no mercado, mais rigorosa é a inspeção e, portanto, o retrabalho mais frequente necessário. Isso apenas aumenta seu custo.
As inspeções extras realizadas são trabalhos que não resultam em nenhum valor agregado ao produto. A manufatura pode construir medidores em seus gabaritos e acessórios, um processo de inspeção automática que reduz a possibilidade de produtos defeituosos serem usados (isso é chamado de poka-yoke). Isso é feito para garantir que cada produto seja de boa qualidade.
Acreditamos que o reajuste deve ser considerado um trabalho que não deveria ter existido desde o início. Quanto mais pessoas forem necessárias para inspeção e retrabalho fora do processo, menor será a taxa de valor agregado na planta e mais os custos aumentarão.

Você não pode dizer: “Este produto é caro porque o testamos 10 vezes”. Isso não será aceito no mercado. O trabalho que não agrega valor é apenas uma atividade desnecessária. É algo que deve ser eliminado desde o início.
Mesmo se você omitir a atividade desnecessária no processo de trabalho direto e conseguir alguma redução de mão de obra, se produzir produtos defeituosos, a inspeção e o retrabalho aumentam os requisitos de mão de obra. Se você considerar isso do ponto de vista da redução de custos, o resultado pode sair uniforme ou até mesmo uma perda; esse resultado está longe do objetivo original.
Por esse motivo, pensamos da seguinte maneira:
As inspeções fora do processo e o retrabalho são atividades desnecessárias. Queremos eliminá-los o máximo possível. A inspeção deve ser o mínimo necessário e não é necessário retrabalhar (você inevitavelmente reduz a mão de obra).
É importante estar ciente de que grandes reduções de mão de obra são possíveis, eliminando as operações de inspeção e retrabalho, quando você busca por melhorias.
A inspeção em processo deve ser considerada da seguinte maneira:
É necessário que as pessoas verifiquem a qualidade dos produtos que fabricaram, ou seja, a inspeção 100% em processo. Consideramos o processo de produção seguinte como o cliente, para que nenhum produto ruim seja lançado.
É importante ser criativo com todos os vários aspectos dos métodos de inspeção. Além da inspeção visual ou do medidor, também deve ser considerado criar um “Poka-yoke” (à prova de erros).
Quanto à produção em lotes, como a que utiliza prensas automáticas de alta velocidade, acumulamos, digamos, 50 ou 100 peças sobre a rampa e inspecionamos a primeira e a última peça. Se ambas são boas, seguem em frente e são transferidos para os paletes. Se houver um defeito na última peça, examine de qual peça a falha começou a ocorrer, livre-se delas. Então você deve tomar medidas para evitar que esses defeitos aconteçam no futuro.
Este é um tipo de inspeção total. Mesmo em um processo de produção rápido, você não deve pensar que pode realizar apenas inspeções de amostragem. É importante aumentar a qualidade dentro do processo de produção.
O Objetivo do Inspetor
Considere o conceito de “inspeções realizadas por um inspetor”. O trabalho de um inspetor é determinar se um produto está com defeito. Às vezes, eles pensam que isso basta para passar os resultados de volta à etapa anterior.
Isso não é o suficiente. O inspetor deve ser responsável por analisar o local de trabalho por que a falha ocorreu e, tanto quanto possível, por determinar a causa e interromper a recorrência desse problema.
Eles não devem ser apenas um inspetor que realiza um teste de aprovação ou reprovação. O inspetor deve ser um professor que explica o que estava errado e ensina você a não repetir o mesmo erro.
Por exemplo, se um problema que surgiu foi um erro durante a montagem de peças, a causa pode não ser tão simples quanto “eu fui descuidado”. Pode ter havido muitas causas diferentes. Por exemplo: as peças não estavam alinhadas em sua ordem de montagem, o botão de parada de linha ou o botão de chamada estava muito longe ou as informações da instrução de trabalho eram difíceis de ler.
Sem identificar essas causas e tomar as medidas apropriadas, as falhas não serão reduzidas. O objetivo do trabalho do inspetor não é jogar fora o produto com defeito, mas reduzi-lo a zero. Seu trabalho é avaliado no cumprimento dessa tarefa.
Poka-Yoke (à prova de erros)
Para criar alta qualidade em um processo de produção, precisamos pensar em quais pontos as pessoas precisam verificar, quais locais eles precisam medir ou quando precisam substituir as ferramentas de corte.
Crie maneiras de usar gabaritos e acessórios para que os produtos enviados da etapa anterior sejam verificados espontaneamente. Isso significa que você incorpora o poka-yoke (à prova de erros) no processo de produção para descobrir defeitos.
É importante padronizar o poka-yoke para garantir que, mesmo que as pessoas sejam alteradas, seja produzida uma qualidade estável.

Às vezes, mesmo as pessoas mais cuidadosas podem cometer erros inadvertidos, especialmente quando medem enquanto executam outras tarefas ou fazem a verificação seguindo uma lista de verificação.
É por isso que é importante criar um mecanismo que elimine espontaneamente produtos defeituosos, erros operacionais, ferimentos ou outros problemas, mesmo sem que uma pessoa preste atenção em tudo. A descoberta automática de quaisquer deficiências é “poka-yoke”.
Para explicar o mecanismo do “poka-yoke” um pouco mais especificamente,
(A) Um mecanismo em que os produtos não podem ser montados em gabaritos quando há um erro operacional.
(B) Um mecanismo em que a máquina não inicia quando há um problema com o produto.
(C) Um mecanismo em que a máquina não inicia quando há um erro operacional.
(D) Um mecanismo para corrigir automaticamente erros operacionais antes de prosseguir com a produção.
(E) Um mecanismo para detectar problemas criados no processo anterior.
(F) Se algum trabalho for deixado incompleto, o processo a seguir não será iniciado.
Outros mecanismos além desses também podem ser considerados. Os seguinte podem ser considerados como métodos poka-yoke.
- Sinais … visualizar a falha com lâmpadas e código de cores para facilitar a descoberta.
- Os gabaritos … crie um gabarito que não aceite produtos diferentes ou não funcione quando houver um erro de montagem, etc.
- Autonomação … para parar a máquina quando ocorrer um problema durante a fabricação. Às vezes, isso não é contado como “poka-yoke”.
Poka-yoke é uma parte extremamente importante na construção de qualidade durante os processos de produção. O objetivo é reduzir os problemas a zero. Para atingir esse objetivo, é importante pensar em métodos como os mencionados acima e encontrar os lugares mais fáceis de entender, bem como aqueles com perda mínima, ao estabelecer o “poka-yoke”.
No próximo artigo nós vamos mergulhar na Seção 4 do Capítulo 1 do Manual, onde o tema central é a relação entre redução de mão de obra e Segurança, que como você vai ver, é a prioridade número 1 da Toyota.
Se você está curtindo e lembrou de alguém que também vai amar conhecer esse material, não esquece de compartilhar e de assinar nossa Newsletter. É rápido, simples e de graça, e você nunca mais vai perder nenhum artigo do blog.
Abraços!
Quer ficar sabendo quando tem artigo novo na Leanstart, antes de todo mundo?
É só você assinar a nossa Newsletter! É rápido, simples e de graça, e você nunca mais vai perder nenhum artigo do blog.
[newsletter_form]
Comentários