Retraduzindo o Sistema Toyota de Produção – Parte 5: Redução de mão de obra e Segurança
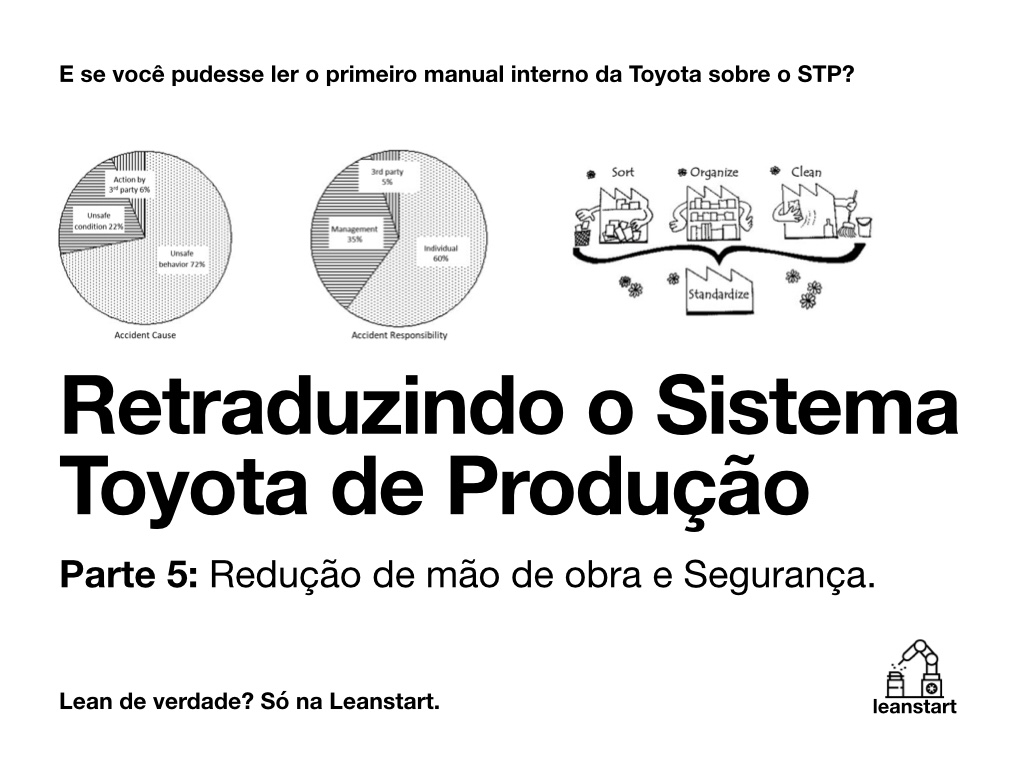
Quer ficar sabendo quando tem artigo novo na Leanstart, antes de todo mundo?
É só você assinar a nossa Newsletter! É rápido, simples e de graça, e você nunca mais vai perder nenhum artigo do blog.
[newsletter_form]
A introdução para a Parte 5 da nossa tradução do primeiro Manual do STP da história da Toyota não poderia ser mais simples:
Segurança é prioridade total é inegociável. É uma questão de caráter.
Por que seria diferente no sistema e na empresa que são símbolos máximos do respeito pela humanidade no processo produtivo?
Mas não pense que você vai encontrar demagogia e mais do mesmo aqui: a Toyota compreendeu a relação entre trabalho e desperdício tão profundamente, que conseguiu encontrar o elo entre redução de desperdícios e o aumento na segurança:
Não se deve esquecer que pessoas, materiais e equipamentos no local de trabalho não são independentes um do outro, mas conectados de maneira complexa.
Seção 4: Redução de mão de obra e Segurança
Primeiro a Segurança
Há um ditado: “Não adianta chorar sobre o leite derramado”.
Vários ativos, como máquinas, mesmo que danificados, podem ser restaurados gastando dinheiro, mas é menos provável que o corpo humano se recupere totalmente depois de ferido. Um desastre fatal, como um acidente que causa a morte, não pode ser compensado com dinheiro.
A segurança deve ser considerada antes de tudo. Não há redução de mão de obra onde a segurança não é considerada. Devemos considerar a segurança como base e, depois, pensar em todas as formas possíveis de redução da mão de obra nesse escopo para reduzir custos.
Às vezes, vemos casos em que a rotina de melhoria não é permitida em nome da segurança. Nesses momentos, precisamos voltar ao ponto de partida e revisar o objetivo do trabalho. Não haverá progresso se você pensar “deixe as coisas como estão”.
A Relação entre Redução de mão de obra e Segurança
Você verá que os valores aparentemente conflitantes de segurança e redução de mão de obra são consistentes entre si, porque a redução de mão de obra significa também promover a eliminação de atividades desnecessárias (Muda), desiguais (Mura) e irracionais (Muri).
A maioria dos acidentes nas plantas de produção ocorre devido a comportamentos que podem ser considerados atividades desnecessárias, desiguais ou irracionais.
Acreditamos que fazer ou ser forçado a fazer coisas desnecessárias ou difíceis de fazer leva a atividades desnecessárias, ações desiguais e sobrecarregadas que acabam sendo prejudiciais.
Poderíamos usar os caracteres japoneses para a palavra “Lesão” para escrever “Isso é estranho se eu mesmo disser”. Comportamentos estranhos que incluem atividades desnecessárias, irregularidades e sobrecargas são a causa de lesões; eliminar atividades desnecessárias, irregularidades e coisas irracionais leva à segurança.
Nos locais de trabalho onde os acidentes são frequentes, o gerenciamento diário é insuficiente. Esses acidentes ocorrem com frequência onde assuntos básicos como 4S [10], procedimentos de trabalho e instruções de trabalho não são considerados ou mesmo irreconhecíveis.

Os locais de trabalho apaixonados por suas rotinas de redução e melhoria do trabalho têm menos acidentes. Quanto mais simplificado o local de trabalho, mais fácil é gerenciar. Enfatizamos o 4S como um aspecto do gerenciamento de segurança. O 4S é baseado nas pessoas, materiais e equipamentos que existem atualmente.
Se o layout das máquinas e equipamentos for mal projetado; então praticar os 4S não alcançará seu objetivo.
Há um limite para o quanto você pode classificar algo quando isso está se movendo em direção à complexidade. Não se deve esquecer que pessoas, materiais e equipamentos no local de trabalho não são independentes um do outro, mas conectados de maneira complexa.
Por exemplo, este ciclo vicioso: há muitas pessoas → muitos produtos (estoque acumulado) → são necessárias mais pessoas para limpeza, carregamento e descarregamento, armazenamento ou retrabalho → ainda mais pessoas.
Aumentar uma coisa aumenta outras coisas no local de trabalho, a complexidade está em proporção direta. É importante promover a gestão da segurança para evitar essa tendência à complicação, tanto quanto possível pela redução do trabalho.
Explicaremos brevemente o 4S; refere-se à classificação, organização, limpeza e padronização.
(A) Classificação (Seiri)
Dividir as coisas em necessárias e desnecessárias e descartar as coisas desnecessárias imediatamente.
(B) Organização (Seiton)
Organizar as coisas necessárias de uma maneira fácil de usar.
(C) Limpeza (Seisou)
Para limpar e manter as coisas arrumadas.
(D) Padronizar (Seiketsu)
Manter o estado de (A), (B) e (C).
A situação atual de acidentes em nossa empresa
Observando o indicador de acidentes de nossa empresa, descobrimos que havia mais de 800 ocorrências de acidentes por ano. Esses acidentes podem ser considerados apenas a ponta do iceberg.
Pode haver ainda mais locais de trabalho em condições semelhantes àquelas em que ocorreram acidentes, bem como aqueles que estão continuamente expostos a perigos, mesmo que felizmente não tenham ocorrido acidentes? Dois anos atrás (1970), 878 acidentes ocorreram.
Se considerarmos a lei de Heinrich [11], provavelmente há um número ainda maior de pessoas que experimentaram situações de quase acidente, mesmo que não tenha terminado em uma. Tais situações perigosas não podem ser deixadas sem melhoria.

Analisando as principais causas de acidentes, bem como as condições de risco da própria causa, descobrimos que houve 142 incidentes em que a segurança não foi levada em consideração; 77 incidentes em que os ajustes de manutenção não estavam sendo feitos e 14 incidentes em que não havia chave de segurança. Isso indica que resta muito espaço para melhorias.

Se você observar o relatório de acidentes, ele mostra muitas lesões causadas pela gestão, relacionadas a problemas na máquina (20%); e o fator mais frequente de acidentes foi o esquecimento de desligar a máquina antes de trabalhar em um problema (30%).
Temos um problema em nossa maneira atual de evitar a recorrência de problemas de equipamento e em nossos sistemas de manutenção preventiva de acidentes.
Um problema por trás de tudo isso; todos os problemas de equipamentos são deixados para o local de trabalho de produção. É necessário abordar os problemas não apenas no local de trabalho, mas também com a gerência.
Os gráficos de mostram o número de acidentes agrupados por fatores principais e a parte responsável. Em 72%, o “comportamento inseguro” é o principal fator para a causa do acidente. O comportamento individual é o fator dominante quando olhamos para a responsabilidade.
Dentro de um fluxo de trabalho simplificado, quase não há movimentos desnecessários, desiguais ou irracionais, tornando-o mais fácil de executar. Também é mais fácil de gerenciar. Nesse sentido, quanto mais simplificado o trabalho, menor será o comportamento de risco.
Isso dá origem à necessidade de “gerenciamento visual” para os líderes. Eles precisam ser capazes de reconhecer imediatamente quando as pessoas realizam ações inseguras e instáveis. É assim que a simplificação está ligada ao aspecto de segurança nas rotinas de redução de mão de obra.
Primeiros passos em direção à um local de produção seguro
Ter um ambiente de trabalho seguro requer uma abordagem em toda a empresa. O primeiro passo é criar um local de trabalho livre de atividades desnecessárias, desiguais e irracionais. Precisamos criar um ambiente em que seja fácil descobrir essas atividades desnecessárias, desiguais e irracionais.
(A) Em que condições o trabalho será realizado?
(B) Que tipo de procedimentos serão executados?
(C) Quanto tempo leva para realizar a atividade?
Um manual de instruções do trabalho que especifique A, B e C deve ser definido (e mantido). Seguir instruções de trabalho eficazes levará à criação de um local de produção seguro.
Nossa conclusão é que promover a redução de mão de obra também levará à segurança. Para criar um local de trabalho seguro, devemos continuar a expandir nossas atividades de redução de mão de obra. Depois disso, gostaríamos de considerar os problemas de autonomação (Jidoka) e ativação com um toque.
Automações simplistas causam lesões
Juntamente com o aumento da produção dos últimos anos, a automação em nossa empresa se desenvolveu rapidamente. Na maioria das vezes, a necessidade dessa automação não foi suficientemente questionada (ou seja, não houve uma investigação completa sobre suas atividades desnecessárias, irregulares e sobrecarregadas), portanto, as quebras ocorrem com frequência. Para piorar, existem máquinas de alta velocidade sem um dispositivo de parada automática, por isso é extremamente perigoso.
Como a automação não foi projetada como Jidoka (ou seja, foi projetada para economizar trabalho, e não para economizar pessoal), ainda precisamos ter alguém para agir como guarda, caso contrário, isso incorreria no risco de a máquina não funcionar como requerido. “Autonomação” significa que uma máquina está equipada com um interruptor de segurança, que para a máquina quando ocorre uma anormalidade. Isso é importante tanto da perspectiva da segurança quanto da redução da mão de obra.
Uma máquina que não pode se parar automaticamente em caso de anormalidade corre o risco de causar acidentes inesperados.
Quanto mais caro o equipamento automatizado, mais nos preocupamos com a danificação, o que acaba em designar pessoas para protegê-lo. As pessoas que o protegem raramente são seus projetistas ou fabricantes, e nem mesmo quem faz sua manutenção, isso aumenta o risco de acidentes.
Por exemplo, considere o seguinte:
Perto de um transportador automatizado, geralmente vemos um sinal que diz: “Desligue o interruptor antes de subir no transportador”.
À primeira vista, chama a atenção para a segurança e parece que a segurança está garantida; mas acima do transportador, existe uma plataforma na qual frequentemente existem barras para mover qualquer coisa presa no transportador.
Uma pessoa pode não querer subir nela, mas, se surgir a necessidade, pode desligar o interruptor antes de subir.
Quando o transportador não pode ser reparado imediatamente (a manutenção pensa que pode esperar, é bom o suficiente se funcionar apenas a 80%). E existe uma expectativa da gerência para garantir que as metas de produção sejam cumpridas. A pessoa ainda seguiria as regras e desligaria o interruptor antes de subir na esteira?
Se ocorrer um acidente, será relatado que a pessoa não seguiu as regras. E a desculpa pode ser dada de que a pessoa não recebeu treinamento suficiente. Mas a verdadeira razão é a presença de equipamentos incompletamente automatizados que foram deixados como estão.
Para equipamentos auto-ativados verdadeiramente automatizados, deve ser estruturado de modo que a execução com 100% de funcionalidade seja garantida, caso contrário, deve ter a estrutura que para automaticamente em situações anormais.
Os 20% de parada do transportador que foram considerados como aceitáveis devem ser considerados como a causa que leva a ferimentos.
Exemplo de uma Fábrica de Máquinas
Veja os fatos de um caso que ocorreu em uma fábrica de máquinas. Casos como esse são comuns em locais de trabalho automatizados.
Nos processos mostrados no diagrama, uma pessoa teve seu dedo cortado por um torno.
Originalmente, o trabalho da pessoa era apenas pegar o trabalho que foi automaticamente organizado em conjuntos e embalá-lo em caixas. Como havia cerca de 10 linhas como a mostrada na ilustração acima, uma única pessoa deveria ter sido suficiente para cobri-las. No entanto, sempre havia três a quatro pessoas em cada linha para melhorar o fluxo; caso contrário, a produção programada não poderia ser atendida.
Como o fluxo através das calhas era irregular e os interruptores “Sem trabalho”, “Passe confirmado” e “Trabalho completo” não eram mantidos adequadamente, quando ocorria uma anormalidade, a máquina não parava.
O acidente ocorreu quando o dedo da pessoa ficou preso em uma máquina que estava funcionando “automaticamente”.
Para este exemplo, uma pessoa que observa esse local de trabalho deve questionar por que uma pessoa não pôde fazer o trabalho. Melhorar o fluxo nas calhas alcançaria redução real de mão de obra, além de criar um local de trabalho mais seguro; e mais importante, um acidente poderia ter sido evitado.
A ativação por um toque é um risco?
Explicamos que o conceito de redução de mão de obra e a direção a que nos dirigimos não são contrários à segurança, mas coincidem com o desenvolvimento das várias condições necessárias para promover a segurança.
No final desta seção, gostaríamos de mencionar um exemplo de prensa de estampagem em que a redução de mão de obra também resultou em melhoria da segurança.
A ativação com um toque para máquinas como prensas de estampagem começou a ser adotada. Na oficina, ela é utilizada há bastante tempo. Isso se deve ao conceito de que o manuseio de várias máquinas é uma realidade e trouxe muitas inovações que consideram segurança.
Se optarmos por um tipo de ativação convencional que use o botão “segure para funcionar” com as duas mãos até que a prensa atinja o ponto morto inferior, esse tempo de espera seria uma atividade desnecessária e o tempo extra de caminhada eliminará os benefícios de manuseio de máquinas em vários estágios.
Por que os botões “segure para funcionar” de duas mãos foram utilizados até agora? Eles foram adotados para atender aos regulamentos de segurança do trabalho. De acordo com os regulamentos de segurança do trabalho, “máquinas como prensas devem incluir medidas para impedir a entrada de partes do corpo na zona de perigo ao usar lâminas ou cortadores. Isso não se aplica a prensas estruturadas para que os deslizadores ou cortadores possam ser imediatamente parados quando uma parte do corpo entrar na zona de perigo.”
O sistema de duas mãos cumpre apenas a última parte deste parágrafo, mas não cumpre o objetivo original. Mesmo se houver um botão nas duas mãos, se houver uma terceira pessoa envolvida, ele não funcionará efetivamente, a menos que a pessoa que fez a ativação tenha notado o perigo.
O problema não é se a ativação com um toque é ruim, mas a máquina está estruturada para poder fazer uma parada de emergência quando uma parte do corpo é detectada na zona de perigo.
O progresso no desenvolvimento de dispositivos como botões de ativação com estruturas de segurança, onde a máquina para imediatamente se algo se aproximar, reduz o risco associado à ativação usando um sistema de um toque. A máquina deve ser parada em caso de falha do dispositivo de segurança.
Melhor ainda seria uma máquina que as pessoas possam usar sem colocar suas partes do corpo perto de qualquer zona de perigo. Tais conceitos foram gradualmente sendo introduzidos em prensas de estampagem e linhas de soldagem automáticas.
Por exemplo, há uma prensa de 250 toneladas equipada com o fio de cobre na parte inferior inferior do obturador. Se algo tocar no fio, o interruptor final interromperá a prensagem.
Existe um novo tipo de máquina de solda automática com uma plataforma ao redor. Ela não funciona enquanto uma pessoa estiver em pé na plataforma.
Ambos são exemplos em que um botão foi convertido em uma operação com um toque. Ainda são dispositivos elementares, com melhorias adicionais, provavelmente seremos capazes de transformar todos os botões de ativação em um toque.
Mesmo que você pare de pensar na racionalização do trabalho, convencido de que não há escolha por uma questão de segurança, você pode notar que existem várias opções de uma maneira segura e racional de trabalhar, apenas voltando ao objetivo fundamental do trabalho.
Esforços contínuos dedicados à criação de métodos de trabalho e sistemas para equipamentos ou dispositivos dentro das margens de segurança, ao escolher aqueles com a mínima atividade desnecessária, certamente se tornarão ainda mais importantes no futuro.
Notas
[10] 4S é retirado de quatro palavras japonesas que começam com ‘S’ – Seri, Seiton, Seisou e Seiketsu. Consultores posteriores adicionaram outros para se tornarem 5S ou 6S, complicando o programa original até que a ferramenta se tornasse um programa independente, sem entender por que ele era útil em primeiro lugar.
[11] Lei de Heinrich – Em seu livro de 1931 “Prevenção de acidentes industriais, uma abordagem científica”, Herbert W. Heinrich apresentou o seguinte conceito que ficou conhecido como Lei de Heinrich: em um local de trabalho, para todos os acidentes que causam ferimentos graves, existem 29 acidentes que causam ferimentos leves e 300 acidentes que não causam ferimentos.
No próximo artigo nós vamos mergulhar na Seção 5 do Capítulo 1 do Manual, onde o tema central é a relação entre redução de mão de obra e as Relações Humanas, onde vamos conhecer como a Toyota lidera para gerar engajamento, através do respeito pelas pessoas.
Se você está curtindo e lembrou de alguém que também vai amar conhecer esse material, não esquece de compartilhar e de assinar nossa Newsletter. É rápido, simples e de graça, e você nunca mais vai perder nenhum artigo do blog.
Abraços!
Quer ficar sabendo quando tem artigo novo na Leanstart, antes de todo mundo?
É só você assinar a nossa Newsletter! É rápido, simples e de graça, e você nunca mais vai perder nenhum artigo do blog.
[newsletter_form]
Comentários