Para fazer Kaizen, SEMPRE temos que mapear processo?

Resposta curta: não.
Nesta semana iniciei uma enquete na página da Leanstart no LinkedIn, e até o momento, o resultado tem me assustado bastante.
Primeiramente, quero agradecer a todos que participam das nossas enquetes. Raramente fazemos alguma, e fico muito feliz em ver que elas tem despertado a vontade de fazer parte em quem passa por elas. Especialmente quando envolvem expor o conhecimento.
E nesta enquete, onde a pergunta foi “Para fazer Kaizen, sempre temos que mapear processo?”, até o momento, 79%-80% dos respondentes escolheram que “Sim”.
Neste texto, vamos explorar juntos um pouco dos motivos de eu ter considerado este resultado como algo extremamente preocupante.
O significado de Kaizen
Um grande veneno no mundo da busca por melhores resultados é que cada um dá o significado que quer para as coisas. Não há uma regulamentação oficial (e se houvesse, dependendo dos reguladores, seria até pior), mas para tentar cobrir este problema, eu mesmo criei a minha: sempre busco os significados, referências e respostas o mais próximo possível da origem do assunto.
E na busca pelo significado de Kaizen, temos que a tradução mais adequada é que Kaizen significa “mudança para melhor”. Porém, fazendo um aprofundamento no ideograma do termo, temos algo bem mais profundo:
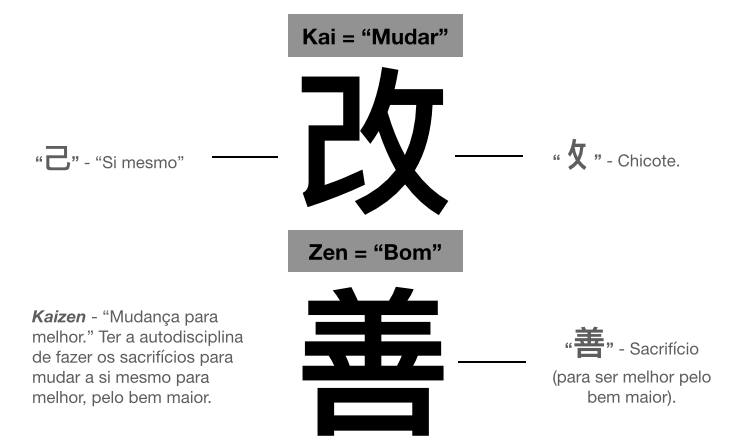
Fonte: K. Anderson / I. Kato / A. Smalley
Na essência, podemos dizer que o Kaizen consiste na autodisciplina de melhorar a si mesmo, fazer este sacrifício, para o bem de todos. Quando você se predispõe a ter mais conhecimento, ser mais eficiente, gentil, cordial, diminuindo seu egoísmo de ficar no conforto de não fazer nada, o mundo passa a ter mais chances de ser mais agradável para todos.
Mas claramente, sabemos que não é com este significado que o Kaizen é vendido por aí.
Do ponto de vista técnico, as atividades que aconteciam dentro da Toyota e que ficaram famosas como Kaizen, antes de terem este nome, eram chamadas de atividades de racionalização.
Alguns significados do verbo racionar:
- transitivo direto
organizar (algo) de maneira lógica, tornando-o mais funcional, prático, eficaz; simplificar.“r. a ortografia” - transitivo direto
organizar (atividade econômica) de forma racional a fim de obter o máximo de rendimento com um mínimo de custo.“r. a produção”
A partir disso, quando pensamos no significado técnico de Kaizen, podemos considerar que este é o processo de simplificar o trabalho, com o objetivo de reduzir os três grandes adversários do trabalho eficiente e de baixo custo: variação, sobrecargas e desperdícios. É mudar o trabalho para melhor, e melhor significa com menos esforço no sentido geral da palavra: físico, mental, financeiro.
No ocidente, infelizmente, houve um efeito colateral indesejado da prática do Kaizen. Para que a visita de consultores japoneses fosse melhor aproveitada, visto os custos de deslocamento, nestas visitas os Kaizens passaram a ser executados de forma concentrada, intensiva, durante uma semana. O efeito colateral foi no nascimento dos eventos Kaizen, e este passou a ser o significado do processo de Kaizen para a maioria: reunir uma equipe, em uma data específica, e fazer todo o um ritual. Não poderia estar mais errado.
Pensando em tudo isso, fica a pergunta:
- Todas as oportunidades de tornar o trabalho mais simples, com menos esforço, realmente demandam que seja criado um mapa do processo?
O que um mecânico faz
Utilizar um exemplo baseado na lógica mecanicista não é saudável, visto que empresas, por conterem seres humanos, idealmente irão funcionar como organismos vivos. Mas aqui a ideia funciona bem.
Imagine que seu veículo está fazendo barulhos estranhos. Muito estranhos. Você então começa a se preocupar, pois parece ser algo grave e consequentemente caro de consertar. Então, você decide finalmente levar o seu veículo até um bom mecânico.
Quando você chega lá, o que este bom mecânico (considerando que ele realmente é bom), faz?
Ele pega uma chave de fenda?
Um martelo?
Troca o óleo?
Não.
A primeira coisa que ele faz é entender o problema, e no geral, a primeira “ferramenta” que ele usa é o conhecimento. Ele vai ouvir o barulho que seu veículo está fazendo, e com base no conhecimento que ele tem de mecânica automotiva, raciocínio lógico, estes processando aquilo que ele percebeu sensorialmente (com tato, audição, visão, olfato, paladar), irão decidir qual ferramenta ou método de diagnóstico ele vai aplicar para compreender melhor o problema antes de fazer qualquer tipo de reparo. A primeira coisa que entra em ação é o cérebro do mecânico.
Mas quando pensamos em Kaizen, o que tenho percebido é que na ânsia por ferramentas que gerem respostas rápidas, certeiras (talvez por pressão inadequada das lideranças), as pessoas passaram a ser dependentes químicas delas. Não conseguem dar um passo sequer, duvidam da genialidade natural que elas possuem simplesmente por serem humanos. Estão sempre esperando por receitas, respostas, e deixam sua máquina orgânica mais poderosa, o cérebro, esquecido. Meu Deus, o que foi que nosso mundo do trabalho, cursos e consultorias fez com nossos colegas?!
O método do Kaizen
Este abaixo é o que considero como o método básico para se fazer Kaizen. Encontrei ele em um material produzido pelo Sr. Isao Kato, que por décadas foi o responsável por toda a sistemática de treinamentos na Toyota, inclusive durante a época de vida do Sr. Taiichi Ohno. O Sr. Kato chegou a tratar pessoalmente com lendas como por exemplo, o Dr. Shigeo Shingo, durante o período em que este ministrou aulas de Engenharia Industrial (não o curso acadêmico), para os supervisores da empresa. É uma lógica bem simples, de apenas 6 passos:

Fonte: A. Smalley / I. Kato
Na internet, você irá encontrar outras variações desta ideia (que na sua maioria, não citam a fonte), e dentre elas, a que gerou a motivação para a pesquisa e para a criação deste texto. Não irei colocar uma imagem, para não gerar nenhum tipo de desconforto no criador, mas em uma imagem com ela, você encontrará o ensinamento de que o “passo a passo” geral do Kaizen seria o seguinte:
- Identificar uma oportunidade de melhoria;
- Mapear o processo atual;
- Desenvolver uma solução;
- Implementar;
- Analisar os resultados;
- Criar um padrão;
- Planejar os próximos passos.
Considerando que mapear o processo atual seja compreendido como criar um mapa de processo, com as etapas de processo, as operações, registrar isso com post-it, colar em uma parede, ou então, criar um fluxo software, ou ainda pior, criar um Mapa de Fluxo de Valor (MFV e em inglês, Value Stream Map (VSM)), fico aterrorizado em imaginar o quanto de oportunidades de engajamento e de retorno moral e financeiro meus colegas andam “deixando na mesa”, e abaixo veremos o motivo.
Um mundo de oportunidades que não precisam de um mapa: apenas bom senso
Observe a seguinte estação de trabalho, onde um operador tem como uma de suas operações, embalar o produto que está passando pela esteira.
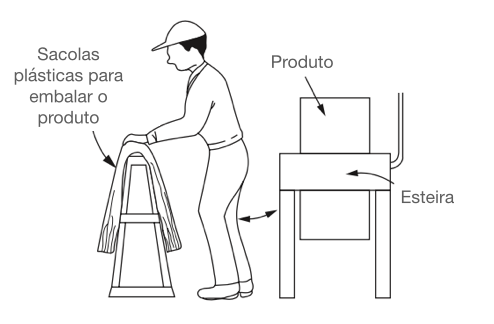
Fonte: H. Hirano
Antes de seguir descendo a página e lendo o texto, pare agora e pense:
- Quais desperdícios você enxerga?
- Como você poderia simplificar este trabalho e facilitar a vida deste operador?
Identificou o potencial de melhoria?
Se esta imagem fosse animada, você veria que o dia todo este operador tem que fazer um movimento de virar de costas para o produto para pegar uma sacola, e então embalar o produto. Com uma noção básica dos conceitos de variação, sobrecarga e desperdício, podemos perceber que há algo estranho, sem lógica do ponto de vista de eficiência acontecendo aqui: há um movimento constante onde o operador troca a posição do seu corpo em relação ao produto para poder pegar uma sacola plástica.
Analisando os métodos atuais
Podemos perceber que este movimento não agrega valor ao produto e gera fadiga no operador. O método atual não posiciona os materiais de trabalho de forma a facilitar o fluxo das operações. Poderíamos medir quantos segundos ele perde por dia neste movimento.
Gerando ideias originais
Poderíamos trocar o local de armazenamento das sacolas plásticas. É uma ideia simples, de fácil e rápida execução. Verificamos e não prejudica a Segurança do operador, nem a Qualidade do produto, aumenta a Produtividade e não afeta os Custos. Pelo contrário: essa troca reduz o número de horas no produto, de forma simples.
Desenvolvemos nosso plano de implementação
Escolhemos uma estação de trabalho que executa esta operação e junto do operador, fizemos alguns testes para chegar na versão adequada da ideia.
Implementamos o plano
Colocamos a ideia para funcionar na prática utilizando materiais de sucata que estavam perdidos pela empresa.
Avaliamos o novo método
Depois de alguns dias rodando a ideia na prática, percebemos e confirmamos que a ideia realmente funciona.
Voilà!

Fonte: H. Hirano
Pergunta:
- Realmente seria necessário fazer um mapa de processo, ou um MFV, para enxergar isso?
Se você estivesse sofrendo para preencher todos os dias uma planilha cheia de cálculos manuais, você precisaria fazer um mapa de processo antes de automatizar a execução, simplificar seu trabalho e parar de sofrer?
Precisaria de um mapa de processo ao perceber ou para perceber que alguém está trabalhando com postura inadequada?
Ou para ver que algum tipo de apoio ajudaria a manter uma peça na posição correta de montagem sempre?
Não se esqueça que o tempo que investimos em uma análise não agrega valor diretamente no produto. É um tipo de desperdício (falamos mais disso aqui neste artigo).

Fonte: Lean Lab Stories
Ah, mas isso é Kaizen pontual!
Um dos argumentos para sair mapeando tudo até sem necessidade é a de que devemos pensar de forma sistêmica na hora de fazer Kaizen. Isso realmente procede, especialmente quando o assunto são grandes mudanças para melhor: a reestruturação do fluxo geral de uma linha de montagem, alterações de layout, planejamento de uma nova unidade, uma nova linha de produto, entre outras, que nem chamamos exatamente de Kaizen muitas vezes, mas sim, de Kaikaku. Mas estas situações não são a regra.
Por outro lado, eu sinto que muitos consultores também são vitimas (ou criminosos intencionais) do mapeamento como “muleta” do Kaizen. Ou para poder parecer que estão fazendo alguma coisa enquanto entendem o processo do cliente (um dono de empresa tradicional não iria gostar de ver o consultor caríssimo aparentemente de bobeira somente olhando o processo), ou para capturar aquelas mudanças drásticas, com base nas quais eles conseguem fazer algum cálculo que gere uma projeção de retorno maior do que os honorários assustadores que a empresa terá que pagar por seu trabalho. Os contratantes não sabem expor seus problemas, e cabe ao consultor achar onde mexer para impressionar com o maior ganho que justifique sua presença. Isso pode ser bom e funcionar para relacionamentos de curto ou curtíssimo prazo entre consultorias e empresas, e portanto, te ensinam “Sempre comece mapeando o processo.”, ou “Faça um VSM.”. Mas na vida real, você provavelmente irá permanecer na empresa por muito mais tempo do que um consultor. Não dá para um negócio viver somente de grandes Kaizens ou Kaikaku.
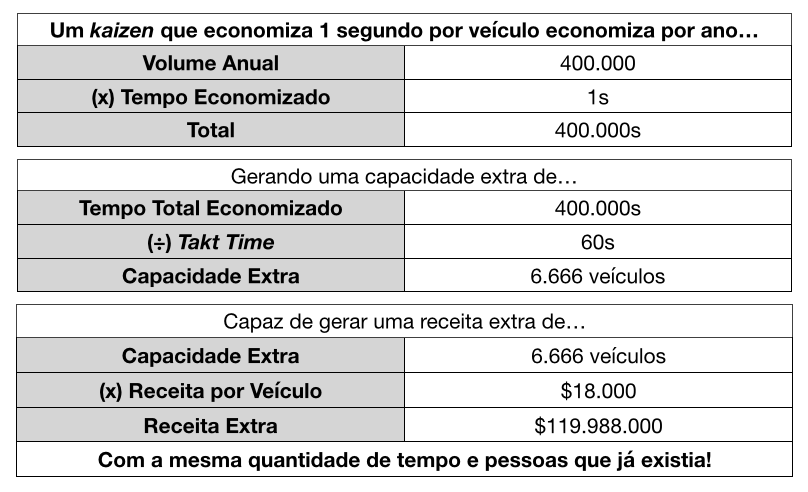
Fonte: D. Wilburn / S. Obara
Pare para pensar um pouco nesta tabela.
Leve em consideração que para gerar a receita extra, seria necessário haver demanda. Mas essa capacidade extra que foi “descoberta” é aquela que parece que falta nos momentos de aumento de vendas, e que faz você ir lá e comprar mais máquinas e equipamentos, investir sem necessidade em um prédio novo, ou contratar mais pessoas para depois ter que demití-las quando a demanda temporária passar. Ela é também aquelas horas que faltam para que seu time se envolva em mais Kaizen.
A planta da Toyota em Georgetown implementou 99% das 80.000 (isso, foram 80 mil) ideias de Kaizen de um determinado período de um ano. Todas ideias geradas pelos colaboradores. Imagine o impacto.
Você tem certeza que quer deixar de lado o potencial de ganho das pequenas e simples ideias em prol daquelas que são mais complexas, e que fazem parecer que somos inteligentes, analíticos e grandes conhecedores de ferramentas?
Quer deixar de lado o potencial das ideias das centenas de pessoas que executam os processos e ficar dependente apenas das ideias das poucas dezenas que gerenciam?
Qual empresa terá mais velocidade de reação em uma crise?
Qual estará mais preparada para uma crise?
E para quando precisar mapear, tenha cuidado!
Não se preocupe, haverá situações onde um mapa de processos irá te ajudar. Mas nestas situações, você tem que tomar cuidado com outro vício: o de achar que os Mapas de Fluxo de Valor são a sua única escolha, a solução, e que sem um bem bonito, você não está fazendo Lean, ou Kaizen, ou o que quer que estejam tentando te vender.
O MFV/VSM é uma ferramenta estratégica. Não deve ser utilizado quando falamos de atuação tática. O MFV/VSM deveria ser feito por e estar na sala da diretoria da empresa, e não no chão de fábrica. Ele mostra uma visão macro de como as coisas acontecem do momento do pedido do seu cliente, a passagem pelo seu fornecedor, até o momento em que tudo isso se torna o produto. Todas essas coisas não são decididas em nível tático. E tenho que concordar com o sensei que diz que deveria não deveria se chamar sequer Mapa de Fluxo de Valor, pois a ideia é enxergar desperdício.

Fonte: Leanstart
Um Fluxo de Valor é composto por Processos, que são compostos de Operações. Muitas vezes, a visão do Fluxo de Valor não é a que você precisa para eliminar variações, sobrecargas e desperdícios. Existem soluções mais adequadas para isso, por exemplo, um mapeamento de processos mais tradicional.
Mas existem mapeamentos e mapeamentos de processo. Alguns são mais uma competição estética e de seguir normas, convenções e modas do que realmente para melhorar processos. Tenha cuidado com isso. Você não necessariamente precisa de um mapeamento para fazer Kaizen, mas todo mapeamento deve gerar Kaizen.
Aqui na Leanstart, temos uma alternativa bem legal, simples e barata para você não cair nessa armadilha.
Nunca se esqueça: você é o elemento mais importante no Kaizen. Toda e qualquer ferramenta externa ao seu corpo serve a você, para aumentar sua capacidade de análise. Mas para ela realmente aumentar sua capacidade de análise, ela depende do seu senso crítico em relação a sua real utilidade. Tenha em mente que quem vai puxar a escolha das ferramentas, e definir quanto tempo vai durar um Kaizen é a complexidade da mudança escolhida. O nome Kaizen não significa que deve durar 1 minuto, ou 5 dias, ou 1 ano. Nem de que deve ser feito por uma equipe, ou individualmente. Muito menos se deve ser utilizada ferramenta A, B ou C. Essa confusão toda sobre o que realmente significa fazer Kaizen surge da vontade sufocante de vender Kaizen enlatado de acordo com a visão ocidental das coisas, de nomear elas demais, empacotar, e ficar dando nome e sobrenome para coisas que geralmente não precisam de nome e sobrenome. Por isso, nunca se esqueça:
- A primeira “ferramenta” a ser utilizada e a única que nunca pode ficar de fora de qualquer Kaizen é o seu cérebro!
Seja como o bom mecânico ou o bom médico (olha aí um exemplo mais orgânico), que antes de escolher como fará o diagnóstico, coloca a cabeça para pensar.
Muito obrigado por ter lido mais este artigo!
Um grande abraço, e até a próxima.
Muito bom artigo!
Muito obrigado, sensei! É uma honra ter o senhor por aqui!
Um forte abraço!