Retraduzindo o Sistema Toyota de Produção – Parte 2: O Método de Redução de Mão de Obra e Custos da Toyota
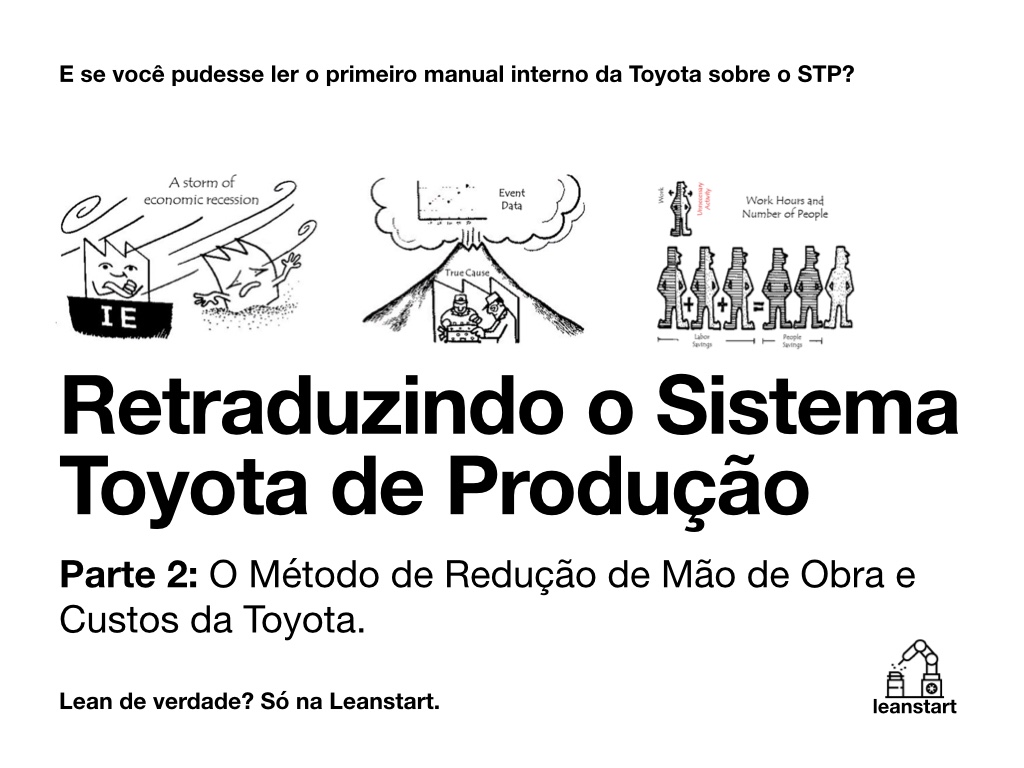
Hora de começarmos a desafiar o senso comum.
No post de abertura da nossa série Retraduzindo o Sistema Toyota de Produção nós demos um mergulho na superfície do pensamento de Taiichi Ohno e aprendemos que todo o sistema foi resultado da busca do objetivo da redução de custos e aumento de produtividade. Isso se deu através da ideia aparentemente absurda de Kiichiro Toyoda (inspirado por Ford) chamada de Just-in-Time. O STP é o resultado da tentativa e erro de Ohno para tornar o JIT possível. Após conseguir um sistema estável, a Toyota precisava colocar foco em criar a mesma estrutura em seus fornecedores.
Mas como Ohno e sua equipe perseguiam esse ideal dentro de outras empresas? Quais mudanças devem ocorrer na forma de pensar e agir no genba para que as bases se estabeleçam? É o que vamos começar a ver agora, na parte 2 da nossa série, e que cobre o Capítulo 1 do primeiro Manual do STP da Toyota.
Capítulo 1
Seção 1: O Método de Redução de Mão de Obra e Custos da Toyota
As ideias básicas do Sistema Toyota de Produção (STP)
O STP é uma sequência de operações com o objetivo de melhorar a produtividade, reduzindo atividades desnecessárias (Muda), irracionais (Muri) e desiguais (Mura), diminuindo assim nossos custos de produção.
Embora suas ideias subjacentes sejam baseadas nas teorias gerais de Engenharia Industrial (EI), essas ideias fundamentais foram desenvolvidas durante um longo período de tempo exclusivamente para a melhoria do sistema de produção da Toyota Motor Corporation. Não é uma aplicação simples das teorias da EI. Em vez de apenas listar fatos sobre as ideias fundamentais desta seção, gostaríamos de revisar as características do STP e demonstrar alguns de seus conceitos.
Engenharia Industrial em toda a empresa e conectada ao gerenciamento
Muito se tem falado sobre sistemas de gerenciamento de produção; não existe um método único para “Como fazer as coisas” que funcionaria em todos os processos de produção de todos os tipos de produtos.
Consequentemente, algumas empresas poderiam fabricar um produto usando uma única pessoa, outras usariam duas pessoas, enquanto uma empresa totalmente despreocupada com os métodos de produção o produziria usando três pessoas.
No último caso, a empresa que utilizava três pessoas provavelmente teria mais armazéns, veículos, paletes, transportadores e outros equipamentos. Isso pode causar um aumento no número de funcionários indiretos e o custo de produção pode ser o dobro (ou mais), fazendo uma grande diferença nos lucros (se é que elas são rentáveis).
Não temos estatísticas concretas que esclareçam essa relação; podemos imaginar que essa diferença ocorra em muitas empresas. Além disso, essa diferença não será apenas uma questão da situação atual. A cada ano, o investimento será repetido de maneira semelhante, porque os planos anuais são projetados com base no pensamento que criou a situação atual.
Uma vez investidos os custos fixos (fábricas, equipamentos, máquinas, etc.), esses custos fixos são irrecuperáveis, mesmo que posteriormente se revelem desnecessários. Considerando os sérios riscos de excesso de investimento, esse é um problema significativo para qualquer empresa.
A única maneira de evitar o risco de investimento excessivo é melhorar continuamente a eficiência da produção em todos os aspectos do processo operacional, reduzindo as unidades básicas de consumo de mão de obra, equipamentos e máquinas. Em seguida, refletir essas melhorias nos planos de produção para a próxima fase.

Olhando para as coisas dessa perspectiva, a Engenharia Industrial terá um grande efeito no gerenciamento de negócios. As empresas que não praticam a EI suficientemente são como castelos esplêndidos construídos na areia. A empresa pode parecer bem-sucedida em tempos de expansão econômica, mas durante as contrações econômicas, pode entrar em colapso como se fosse atingida por um tufão ou um terremoto.
As rotinas de melhoria de produtividade são uma base essencial do sistema de gerenciamento corporativo da Toyota. Todos os departamentos envolvidos na produção lidam com as coisas da maneira mais eficaz possível. O sistema de produção é baseado nos seguintes conceitos:
Nivelamento dos planos de produção (Heijunka)
Se você pensa unicamente na eficiência da produção na planta de montagem final, pode pensar que é mais eficiente para a planta executar apenas um produto; isso vai resultar em atividades desnecessárias nas etapas anteriores da produção.
Diminuição no tamanho dos lotes
Os lotes devem ser minimizados nos processos típicos de produção em lotes, como o uso de uma prensa de estampagem. Não se trata apenas de acúmulo de inventário ou aumento da mão-de-obra para o transporte, mas há o risco de ocorrer indisponibilidade de produto, causado por prioridades erradas dos pedidos. E a capacidade dos processos pode ser julgada inadequadamente como insuficiente, o que levaria a uma ampliação desnecessária das linhas de produção.
Para habilitar a produção de pequenos lotes sem causar uma redução em sua capacidade de produção ou adicionar custos, é necessário melhorar sua capacidade de setup.
Just-in-Time
Produza apenas os itens necessários, no tempo e na quantidade necessárias. O objetivo disso é reduzir a atividade desnecessária de superprodução, além de permitir que você visualize a capacidade excedente naquele momento.
Atitude Científica
No local de trabalho, a solução de problemas deve seguir claramente as seguintes etapas: a situação real é o ponto de partida, investigue a causa raiz e desenvolva uma solução. Quando se trata de local de trabalho, os fatos são considerados mais valiosos.

Por exemplo, independentemente da quantidade de dados apresentados, é difícil compreender a situação real do local de trabalho a partir dos dados. Se um defeito ocorrer, descobrir dados (relatórios) significaria um atraso na tomada de contramedidas.
Pior ainda, devido ao erro de reconhecimento da verdadeira causa da falha, você também pode deixar de impedir a recorrência da falha. Não há lugar melhor do que o local de trabalho real onde você possa entender adequadamente a situação real do que está acontecendo lá. Quando há uma falha, você pode contê-la imediatamente; é mais fácil encontrar a causa verdadeira e tomar medidas imediatas.
No STP, quando se trata de local de trabalho, consideramos os fatos reais como mais precisos que os dados. Quando você tem um problema e seu processo de descobrir a causa raiz é insuficiente; as contramedidas que você criar também estarão fora de foco. É por isso que é necessário usar o método 5-Porquês e se perguntar “Por que, por que, por que …”, até encontrar a causa raiz. Para fazer esse método funcionar, lembre-se dos seguintes pontos:
Torne os detalhes dos problemas algo óbvio
Se o problema for conhecido, é relativamente fácil implementar contramedidas. A parte difícil é descobrir qual é o verdadeiro problema. É por isso que usamos várias ferramentas para sinalizar um problema.
O objetivo da resolução de problemas deve ser claro
A melhoria é baseada na necessidade. A causa raiz deve ser identificada e resolvida. As contramedidas tomadas sem investigar completamente a causa raiz seriam apenas uma medida provisória, que não leva à prevenção de reincidência do problema.
Defina contramedidas para todas as falhas
Mesmo para a falha que ocorre apenas uma vez em 1000. Quando você tem fatos, pode investigar sua causa e tomar medidas preventivas. É vital poder detectar os defeitos pouco frequentes que provavelmente passam despercebidos.
Seja prático
Existem dois aspectos em ser prático. Primeiro, a abordagem deve ter medidas passo a passo. Você pode definir uma meta alta, mas seu progresso em direção a essa meta deve ser realizado passo a passo. O segundo é atribuir importância aos resultados.
Com base nessas ideias, pensamos da seguinte forma:
Comece da melhoria do trabalho para a melhoria do equipamento
A sequência geral é: melhoria das pessoas (treinamento), processo (incluindo layout), equipamento e design. (Mais detalhes na Seção 6)
“Horas-homem”, “número de pessoas”, “economia de custos de mão-de-obra” e “economia de mão-de-obra”

Nos cálculos, você pode dizer que economizou 0,1 hora ou 0,5 hora. No entanto, você ainda precisa de uma pessoa, mesmo para o trabalho de 0,1 hora. Se um emprego para uma pessoa for reduzido em 0,9 horas, isso não resultará em uma redução nos custos de mão-de-obra. Somente quando o número de pessoas for reduzido, será alcançada uma verdadeira redução de custos. A melhoria do trabalho deve se concentrar na redução do número real de pessoas necessárias. [5]
No caso de introdução de equipamento automatizado, se você conseguir 0,9 no valor de trabalho de redução de mão-de-obra, o trabalho de 0,1 pessoa permanecerá (geralmente para vigiar as máquinas), nenhuma redução de pessoas será alcançada, apesar do investimento em equipamento. Isso às vezes é chamado de economia de trabalho; uma redução do número de trabalhadores efetivos que leva a uma redução prática de custos é diferente de “economia de trabalho” e é chamada de “economia de pessoas”.
A diferença entre “automação” e “autonomação”
Com a automação, uma máquina pode funcionar por si mesma, mas ainda precisa de uma pessoa assistindo para parar a máquina quando algo der errado. Quando a autonomação é adicionada à máquina, ela pode detectar os mesmos problemas que a pessoa que estava protegendo a máquina e parar automaticamente a máquina quando um problema foi detectado (detalhes no Capítulo 2).
Verificar (Check) é refletir
A melhoria é concluída quando os resultados pretendidos são obtidos. Quando você não obtém resultados, geralmente é por causa de trabalho inacabado.
Experimente a ideia de melhoria no local de trabalho para ver como ela funciona; verifique os resultados; melhore as coisas ainda não estão funcionando corretamente e verifique novamente. Repetindo esse processo, suas melhorias podem fornecer resultados favoráveis.
O processo de verificação é uma etapa para refletir sobre os resultados do seu trabalho, em vez de simplesmente implementar ideias.
Eficiência econômica é o critério
O objetivo é a redução de custos. A base da avaliação é “se isso é economicamente benéfico ou não?” Quanto ao pensamento prático, temos os seguintes pontos:
A taxa de operação do equipamento é decidida pela quantidade de produção necessária
Isso é enfatizado para evitar cair na maneira errada de pensar sobre o conceito de custos irrecuperáveis, o que sugere que você deve fazer pleno uso das instalações que já foram compradas, ou isso levará a perdas.
Pela mesma razão, no caso de manuseio de várias máquinas, seguimos o mesmo conceito ao focar no trabalho das pessoas, não nas máquinas. (Mais detalhes são discutidos na Seção 2 e no Capítulo 2)
Excesso de capacidade permite que você pratique
As pessoas que têm horário fixo de trabalho receberão o mesmo salário, independentemente de não terem o que fazer (fingir trabalhar) ou de estarem praticando a melhoria do processo de setup quando não tiverem trabalho útil a fazer. (Mais detalhes na Seção 2)
Entendimento claro do papel do local de trabalho
Consideramos todo o local de trabalho como um único organismo. O local de trabalho não é apenas um grupo de mãos que confiaram seus cérebros à gerência. Essencialmente, o local de trabalho deve desempenhar o papel principal. É inaceitável que a engenharia atue como chefe do local de trabalho real. O importante é enfatizar a ação autônoma do local de trabalho.
Para esse fim, a divisão de engenharia deve cumprir seu papel, apoiando os pontos fracos no local de trabalho real, onde eles não têm informações ou habilidades. Eles devem fazer isso sem enfraquecer a responsabilidade no local de trabalho.
Enfatize a capacidade de adaptação às mudanças
Os planos podem mudar frequentemente; o que importa é ter um sistema de produção que possa se adaptar imediatamente quando os planos mudarem. Um local de trabalho adequado, é capaz de lidar com isso.
Notas
[5] A redução do número de pessoas deve ser contextualizada. Quando Taiichi Ohno começou a desenvolver ativamente o STP, a Toyota precisava de cerca de nove vezes mais pessoas para produzir um veículo do que a Ford. Você verá a eficiência da produção como um tema central um em todo o STP e eles fazem isso contando o número de pessoas necessárias para realizar o trabalho.
No próximo artigo nós vamos mergulhar na Seção 2 do Capítulo 1 do Manual, onde o tema central é o aprofundamento na relação entre redução de mão de obra e custos.
Se você está curtindo e lembrou de alguém que também vai amar conhecer esse material, não esquece de compartilhar e de assinar nossa Newsletter. É rápido, simples e de graça, e você nunca mais vai perder nenhum artigo do blog.
Abraços!
Quer ficar sabendo quando tem artigo novo na Leanstart, antes de todo mundo?
É só você assinar a nossa Newsletter! É rápido, simples e de graça, e você nunca mais vai perder nenhum artigo do blog.
[newsletter_form]
Olá Bruno, td bem?
Gostaria de adquirir esse Manual que esta servindo como base a você.
Onde encontro?
Mais uma vez, gostaria de parabeniza-lo pela sua dedicação em trazer ao publico esse conhecimento e outros tão importantes.
Olá Sérgio! Tudo bem aqui, e por aí?
A versão em inglês do manual está disponível gratuitamente no site da Duxinaroe Academy (https://duxacademy.duxinaroe.com/courses/take/tps-handbook-1973/texts/4900215-practice-rather-than-theory-introduction-by-ohno-san). Está em formato de curso, e você pode fazer o login com seu perfil do LinkedIn.
Estou traduzindo ele na integra, aproximadamente um capítulo por dia. Logo deve estar completo aqui no blog.
É uma grande satisfação ser reconhecido por um profissional de tamanha experiência como você. Muito obrigado por me incentivar nessa missão!
Abraços!