Retraduzindo o Sistema Toyota de Produção – Parte 1: “Prática ao invés de teoria”
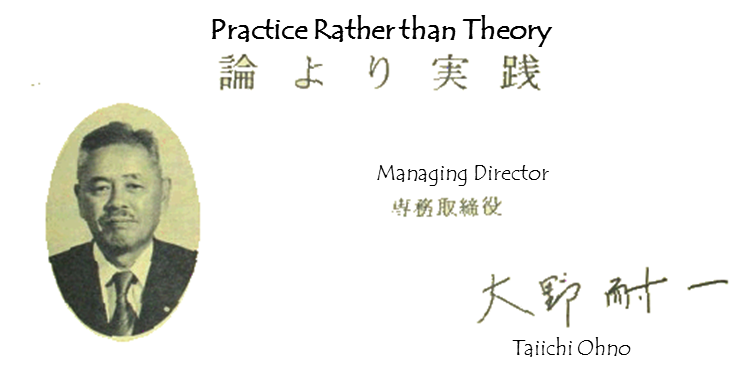
Existem muitos componentes da nossa própria história como civilização ocidental que dificultam o processo de substituição dos pensamentos tradicionais de gestão pelo pensamento progressista iniciado com Frederick W. Taylor.
Mas quando paramos para estudar com afinco sobre o Sistema Toyota de Produção e o Toyota Way, percebemos que uma outra parte da maioria dos nossos problemas graves que comprometem as jornadas Lean estão relacionados ao fato de termos nos distanciado das origens.
E hoje eu vim dividir com você o privilégio que estou tendo de ler o primeiro manual escrito sobre o Sistema Toyota de Produção. Encontrei essa chance única de me conectar com os pensamentos originais de Taiichi Ohno através de um texto de David Bovis, que me levou até a Duxinaroe Academy, e não pude perder a chance de traduzir para o português. Apesar deste trabalho de tradução, todo o crédito deve ser dado a Mark Warren e à equipe que trabalhou com carinho na tradução da versão em japonês para o inglês.
Logo na introdução do manual, Ohno nos dá uma lição importante sobre teoria e prática, com a frase “Pratice rather than theory”.
Mas quando ele diz “Prática ao invés de teoria”, não é no sentido de que a prática é superior, e nem que devemos tentar separar essas duas coisas complementares e inseparáveis. O que precisamos entender para compreender a intenção dessa frase está em outro parágrafo, logo em seguida:
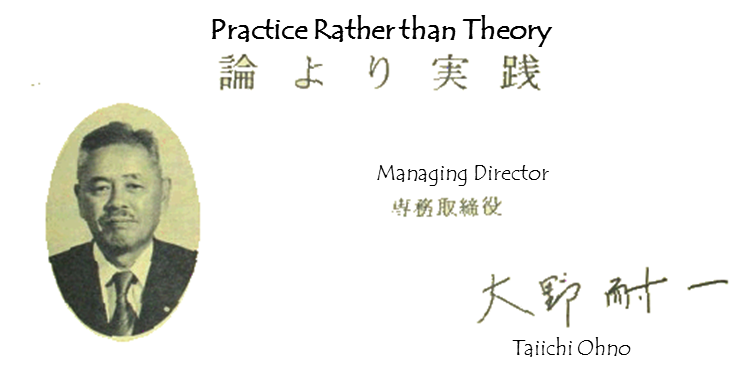
Quando você tenta fazer algo tão óbvio (o Just-in-Time), colide com vários problemas, tornando-o inviável. Mesmo que os ideais sejam assim, se dissermos que são ideais irreais, isso é tudo o que podem ser.
Considerando que o ideograma “理 (lógica)” em “合理化 (racionalização)” é o mesmo “理” de “理想 (Ideal)”, para alguém que está se esforçando para racionalizar, tudo se resume à implementação [para atingir um estado ideal?] ou um desafio sobre o quão perto você pode chegar dele.
Taiichi Ohno
Ao dizer “Pratice rather than theory”, Ohno deixava a mensagem de que tudo o que parece perfeito e impossível continua sendo apenas perfeito e impossível quando você escolhe apenas aceitar, ao invés de ir para a prática e encontrar uma forma de tornar aquilo algo cada vez mais próximo de realidade. Talvez essa seja a versão de Ohno para a frase de outro grande homem, e que foi inspiração direta para o seu trabalho:
Se você acha que pode, ou acha que não pode, você está certo.
Henry Ford
De fato, quando olhamos a situação da Toyota na época, Ohno não tinha tempo a perder lamentando se algo parecia ser só um ideal impossível, mas sim, somente para aprender na prática a como tornar ele menos impossível. O resultado dessa insanidade, você já sabe: a Toyota ser o que é hoje, para quem compra carros, e para quem administra empresas.
Este será o primeiro de uma série de artigos periódicos aqui no blog da Leanstart, onde você vai poder conferir todo o material na integra. A tradução seguirá viva e sendo aprimorada, então se você encontrar pontos de melhoria nela, é só contribuir aqui nos comentários. Sua ajuda será muito bem-vinda. Espero que essa volta às origens seja tão gratificante para você, quanto tem sido para mim, e que sirva de inspiração e luz na sua jornada do kaizen.
Introdução da Tradução – por Mark Warren
Em 1970, a Toyota tinha um sistema de produção bastante estável internamente e eles decidiram ajudar os fornecedores compartilhando seus conhecimentos e habilidades. Para fazer isso, a Toyota criou um grupo especial de aprimoramento interno chamado Divisão de Pesquisa de Produção (posteriormente renomeada para Divisão de Consultoria de Gerenciamento de Operações – OMCD).
O compartilhamento do STP começou com 17 fornecedores, alguns cativos, em 1970. A decisão foi provavelmente porque seus fornecedores externos eram os principais contribuintes para interrupções no fluxo da Toyota; causados por problemas de qualidade, entregas atrasadas, etc. Seu objetivo inicial se concentraria em criar estabilidade, em vez de criar a estrutura que criou seu próprio sistema.
Ohno resistiu a escrever qualquer coisa sobre o STP, portanto a implementação do conhecimento e das habilidades foi aleatória. A dificuldade em compartilhar o pensamento por trás do STP e seu hábito de padronizar todo o trabalho pode ter sido o fator determinante para codificar o pensamento por trás do STP. Em 1976, eles haviam desenvolvido um processo estruturado de introdução e implementação. [3]
Este manual de 1973 também foi usado como material de curso por Ohno e sua equipe – a Associação Japonesa de Administração compilou seus materiais e lançou-o como um livro em 1978. A Productivity Press o traduziu e o lançou como Kanban: just-in-time na Toyota em 1986. Embora grande parte do livro seja composto pelos mesmos materiais do Manual STP de 1973, ele não é apresentado na mesma ordem.
Esta é uma versão anotada (rascunho) que foi traduzida do japonês, para que você possa ter acesso ao mesmo tipo de explicação por trás das idéias dos fornecedores originais.
Traduzir e editar este manual foi apenas um passo na jornada para entender melhor como Taiichi Ohno desenvolveu o sistema de produção da Toyota. Embora o manual tenha fornecido alguma clareza, também ficou claro que havia muito mais informações básicas necessárias para uma implementação bem-sucedida.
As habilidades do TWI são mencionadas especificamente de forma breve, e os elementos dos programas estão logo abaixo da superfície em todo o Manual do STP. A jornada para reunir um roteiro simplificado em que podemos replicar o progresso de Taiichi Ohno em seus anos de desenvolvimento (1950-1965) levou quase o mesmo tempo, mesmo com toda a literatura “lean” disponível. A parte demorada não é fazer com que uma empresa pareça a Toyota ou pareça lean, mas sim, entender os princípios básicos por meio de implementações reais e testar se nossas suposições estavam corretas (método científico de testar sua hipótese).
Descobrimos que muitas camadas de aprendizado estavam ocultas na jornada de Ohno antes do intenso período de crescimento de 1950-1965. Isso inclui a compreensão dos princípios de fluxo, bem como a implementação das habilidades do TWI para construir a base para o trabalho padronizado. A experiência fez dele um pragmático ao trabalhar em direção ao seu ideal; “… para alguém que luta pela racionalização, tudo se torna sobre implementação ou um desafio sobre o quão perto você pode chegar disso.”
Conhecer as camadas ocultas (desenvolver consciência, construir entendimento, criar padrão, desenvolver melhorias e acompanhar) aumentará suas chances de sucesso.

[3] “Toyota Kaizen Methods: Six Steps to Improvement”. Isao Kato e Art Smalley. Os possíeis autores do Manual do STP são Fujio Cho, K. Sugimori, S. Uchikawa, com edição de Isao Kato.
Introdução do Manual do STP – por Taiichi Ohno

Lendo agora, eu acho que o que tentei de várias maneiras ao longo dos anos […] pode ser chamado de trabalho duro.
O falecido presidente, Kiichiro Toyoda, observou que, para essas indústrias em geral, o melhor é que cada peça se apresente ao lado da linha de montagem de forma “Just-In-Time”.
Quando você tenta fazer algo tão óbvio, colide com vários problemas, tornando-o inviável. Mesmo que os ideais sejam assim, se dissermos que são ideais irreais, isso é tudo o que podem ser.
Considerando que o ideograma “理 (lógica)” em “合理化 (racionalização)” é o mesmo “理” de “理想 (Ideal)”, para alguém que está se esforçando para racionalizar, tudo se resume à implementação [para atingir um estado ideal?] ou um desafio sobre o quão perto você pode chegar dele.
Just-in-Time, produtividade, custo e transferência da carga para a terceirização; a julgar pela lógica comum, acredita-se que todos esses aspectos estejam cheios de aspectos contraditórios. Devemos quebrar esse muro da lógica comum e fazer com que esses pontos mutuamente contraditórios coexistam através do que hoje chamamos de “fuga da lógica”.
“Just-In-Time” foi traduzido para o local de trabalho como: “Vá buscar o que você precisa, na quantidade que você precisa, quando precisa” (no departamento que você precisa).
O processo a seguir busca no processo anterior, e como é o fabricante que fornece as peças terceirizadas, indicamos o número a ser fornecido, bem como a data de entrega. Essa é a ideia fundamental do Sistema Toyota de Produção, e essa ideia foi realizada expandindo-o de várias formas.
Como etapa preliminar, a produção correspondente a isso deve ser realizada de maneira mais econômica. No processo anterior (local de trabalho de produção), qualidade, quantidade e custo podem ser facilmente considerados separadamente. Entre qualidade ou garantia da quantidade, é fácil enfatizar a quantidade, principalmente se o custo for enfatizado.
No passado, chamei a técnica de equilibrar essas três (qualidade, quantidade e custo) de “técnica do local de trabalho”. Alguns chamam de “técnica de fabricação”. Recentemente, também me referi a “Engenharia Industrial ao estilo Toyota” como “MIE (Engenharia Industrial Moukeru)”. [4]
Pondo de lado os nomes, uma vez que algumas partes deste sistema estão longe da sabedoria geral convencional (senso comum), fazê-lo de maneira incompleta criaria facilmente o efeito oposto, portanto, ele deve ser realizado minuciosamente. Eu devo mudar minha maneira de pensar e minha perspectiva.
Assim como a maioria dos truques de mágica tem suas próprias técnicas, essa tecnologia no local de trabalho também tem seus truques. Se eu revelasse esse truque, diria que é a repetição de “eliminar atividades desnecessárias – e fazê-lo completamente”, “desenvolver olhos que possam encontrar a atividade desnecessária para que você possa eliminá-la” e “pensar no método para eliminar as atividades desnecessárias que você encontrou. ” Nunca perdendo o vigor ou desistindo, não importa quanto tempo você leve, não importa o quão longe você deva ir.
Notas
[4] Notas do tradutor (Warren) – MIE é uma abreviação de “Moukeru IE” ou “Moukeru Industrial Engineering”. O verbo “moukeru 儲 け る” significa “ganhar dinheiro / lucros”. Em japonês, um verbo modifica o substantivo que o segue, assumindo o significado “A engenharia industrial de ganhar dinheiro”.
No próximo artigo nós vamos mergulhar no Capítulo 1, Seção 1 do Manual, onde o tema central é o método da Toyota para redução de trabalho e custo. Nele, existe uma visão extremamente peculiar sobre o pensamento da Toyota em relação à mão de obra.
Se você está curtindo e lembrou de alguém que também vai amar conhecer esse material, não esquece de compartilhar e de assinar nossa Newsletter. É rápido, simples e de graça, e você nunca mais vai perder nenhum artigo do blog.
Abraços!
Quer ficar sabendo quando tem artigo novo na Leanstart, antes de todo mundo?
É só você assinar a nossa Newsletter! É rápido, simples e de graça, e você nunca mais vai perder nenhum artigo do blog.
[newsletter_form]
A passagem que cita a “racionalização” e o “ideal”, retrata bem o espírito do Kaizen na Toyota. O ideal é algo inalcançável, utópico. Cada vez que aproximamos, ela se apresenta mais à frente do ponto anterior. Isso demonstra a nossa evolução. Esforçamos para aproximarmos um pouco mais dela (isso é permitido).
Ohno falou sobre isso no filme apresentado pelo Hayashi Nampachi.
“…no Sistema Toyota, não há um único item que possamos dizer que já basta… para a Toyota é um eterno aprendizado…”.
Inspirador.
Com certeza, Jorge. O espírito do kaizen age como o antídoto para a nossa preguiça mental diária. Ao longo do manual, isso fica ainda mais explícito.
Thanks for sharing 🙂
Such an honor to have you here, Mr. Bovis! Thank you very much for your kindness and for gifting us with such a treasure. Your work makes the dream of a better world to live and work something possible! 😀