Kaizen na Moda: Melhoria Contínua e Respeito pelas Pessoas na fabricação de roupas
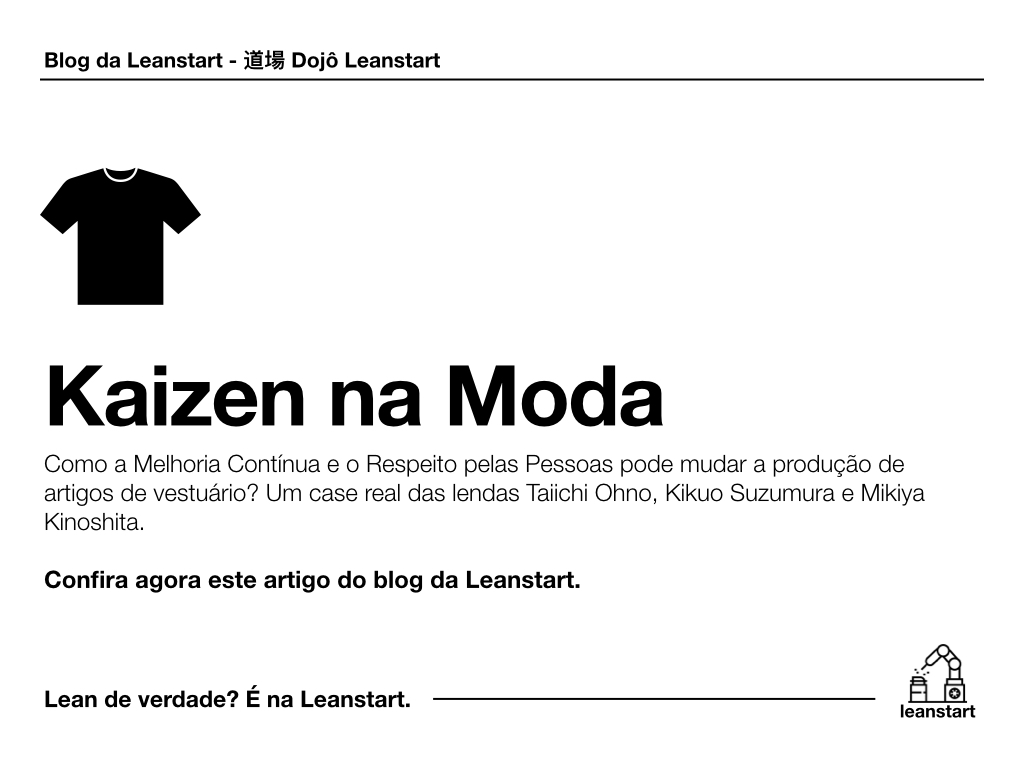
Nós não produzimos obras de arte. Com arte, o preço aumenta conforme o tempo passa. Com nossos produtos, aquilo que já saiu da estação não é muito diferente de “roupa usada”. Você não consegue vender nem pela metade do preço. Roupas masculinas não são tão sensíveis à moda. Mas roupas femininas, ninguém compra depois que já estão fora do estilo. A indústria da moda tem altos e baixos. – Sr. Hirotoshi Hatasaki, presidente da The World Company
Podemos dizer que essa fala do Sr. Hatasaki resume muito bem um dos maiores desafios da indústria da moda, em especial quando o assunto é a parte industrial do processo.
Como conseguir lucrar de forma saudável com essas sazonalidades?
Como reduzir os custos, e evitar descontos e queimas de estoque pelo excesso de estoque, causado pela ilusão da economia de escala?
Como não terceirizar tudo para a China?
Após deixar a Toyota, o Sr. Taiichi Ohno seguiu fervorosamente na prática e aprimoramento da sua filosofia de gestão, nas mais variadas indústrias. Sua jornada acabou, em um determinado momento, resultando na sua posição de conselheiro supremo no NPS – New Production System, uma associação de pesquisa liderada pelo Sr. Ohno, Sr. Kikuo Suzumura (braço direito de Ohno na Toyota) e o Sr. Mikiya Kinoshita, ex-presidente da Ushio Electric. O propósito do NPS era avançar a filosofia do Just-in-Time e aprimorar sua prática dentro das empresas escolhidas para compor a associação. A história do NPS, sua filosofia de trabalho e resultados são uma jóia desconhecida a parte, que com certeza vai acabar se tornando um artigo no blog da Leanstart, dado a riqueza de sabedoria e à minha sorte de conseguir para a minha biblioteca o provavelmente único e raríssimo livro escrito sobre eles na história.
A The World Company, empresa da qual o Sr. Hatasaki era presidente, era uma das empresas membro do NPS. Fazer parte dessa associação e conseguir a consultoria da lenda não era um processo nada fácil: os líderes do NPS não aceitavam pedido de consultoria a não ser que o presidente da empresa pedisse pessoalmente, e mostrasse na prática que estava comprometido e disposto a mudar tudo. Era comum ter que tentar uma dezena de vezes, até convencer o NPS de que você merecia o tempo deles. Interessante esse contraste com o que vemos hoje, onde todos somos consultores, e somos nós quem imploramos para melhorar o negócio dos outros. Sem dúvida, um grande filtro de comprometimento.
Mas uma vez parte do NPS, e se disposta a aprender, uma empresa realizava feitos que pareciam milagres através do kaizen, e neste artigo, vamos observar o contraste que a aplicação sistemática dos conceitos do Sistema Toyota de Produção gera em uma empresa.
Costurar em pé é loucura?
O senso comum é um grande veneno para a necessidade de melhorar a produtividade. Esse “conjunto de ideias e opiniões que é aceito pela maioria das pessoas de um grupo ou sociedade, geralmente imposto e desprovido de valor crítico” precisa ser desafiado todos os dias. E um item que sofre diante do senso comum é a questão do trabalhar em pé.
Em uma confecção tradicional, a tendencia é encontrarmos nossa operação sentada diante de suas máquinas. Além de imaginarmos que é ergonomicamente ideal, acreditamos estar proporcionando conforto e qualidade de vida no trabalho para nosso ativo mais valioso.
Mas se você visitasse a The World Company na época de adoção da filosofia do NPS, não iria encontrar operadores de máquinas de costura sentados, e muito menos, um em cada máquina. Você veria um sistema semelhante à rotina de uma dona de casa dos filmes: ela coloca o arroz no fogo para cozinhar. O cozimento leva tempo, mas ela não desperdiça sua vida olhando o arroz cozinhar, e sim, enquanto isso, prepara a salada, ovos, e outras atividades, até o momento de juntar os itens na mesa do almoço ou do jantar. Pois é: a vida cotidiana está cheia de exemplos práticos que aparentemente esquecemos ao passar do relógio de ponto na empresa.
Fazendo uso dos princípios da operação multitarefa, semelhante ao exemplo acima, um operador agora era responsável até 4 máquinas de costura. Se antes você precisava de 20 pessoas para rodar 20 máquinas, agora você precisaria de apenas cinco. As outras 15 pessoas poderiam ser dedicadas para novas linhas de produto, internalização de itens que antes eram comprados, e times de kaizen, por exemplo. Lembre-se: o kaizen nunca deve gerar demissões.
A altura de cada uma das máquinas foi adaptada internamente para se adequar ergonomicamente à nova posição de trabalho, seguindo a filosofia de não gastar dinheiro sem necessidade, com por exemplo, a compra de máquinas novas mais adequadas. Esse tipo de operação, apoiada pelo conceito do Jidoka, onde as máquinas foram melhoradas com mecanismos simples para interromper automaticamente o trabalho ao surgir um problema – por exemplo, o rompimento de uma linha – foi o que permitiu que nenhum operador precisasse desperdiçar sua vida assistindo o equipamento trabalhar, mas sim, que pudesse dedicar seu conhecimento e energia em outra atividade geradora de valor para os clientes, contribuindo para a prosperidade de todos. E tudo isso, combinado com o conceito de célula de fluxo, onde o operador não estava operando grupos de equipamentos que fazem a mesma coisa, mas sim, um grupo de equipamentos onde um costurava colarinhos, outro mangas, outro a parte frontal. Isso é um grande contraste em relação ao método tradicional, onde temos ilhas de operadores agrupados, especializados em determinadas operações, e desconectados da construção geral do produto.
Você deve estar pensando no tamanho da resistência dos operadores com a sugestão de trabalhar em pé, e realmente, e obviamente, ela existiu. Alguns acusaram a The World Company de estar abusando e explorando as pessoas. O senso comum não tem preconceito em relação a cargos e afeta igualmente a todos que trabalham em uma empresa.
Mas seguindo a ideia de um pequeno passo de cada vez, primeiro convenceram um pequeno grupo de pessoas a testar o novo método. Após esse teste, o pequeno grupo percebeu que trabalhar em pé não só era mais saudável, como se movimentar e ser capaz de executar várias tarefas diferentes tornava o trabalho muito mais agradável do que permanecer o dia todo sentado, costurando o mesmo tipo de componente de peça de vestuário o dia todo, como um robô. Muita gente tem o preconceito de que a padronização e outros mecanismos necessários para a produtividade desumanizam o operador, quando na verdade, quem desumaniza é o modo como é utilizado: com a mentalidade tradicional de liderança. É ela quem robotiza e desumaniza as pessoas. Depois da adoção deste pequeno grupo, o novo método se espalhou positivamente pelo restante da operação.
“Quando uma pessoa é alocada em uma tarefa especializada, uma pessoa pode acabar ficando ociosa enquanto o trabalhador ao lado está acelerado. Isso não acontece quando temos operação multitarefa (sistema nagara seisan, ou ‘produção baseada em fazer algo enquanto faz outra coisa’) Se temos 20 processos, não precisamos de 20 especialistas. Ao invés disso, provavelmente teremos seis ou menos operadores cuidando de três ou quatro processos. Isso significa não termos mais esperas. Os produtos estarão sempre se movendo. Não haverá pilhas de produto semi-acabado. Defeitos também poderão ser percebidos pelos operadores. Cada dia de trabalho produz apenas produto acabado. O (excesso) Work-in-Process é eliminado.
Quando você utiliza uma produção em linha e restringe os trabalhadores a trabalhos especializados, eles passam a acreditar que só conseguem fazer tarefas especializadas. Estamos tentando desenvolver operadores multitalentosos. […] Se você faz a mesma coisa o dia todo, todos os dias, o trabalho começa a ficar tedioso. Por outro lado, se você está envolvido em cada estágio da produção do começo ao fim, o trabalho se torna mais agradável e com sentido. Fazer todo dia a mesma coisa é chato. Um operador multi-talentoso sabe como está contribuindo. Ele começa a inovar.” – comenta o Sr. Hatasaki
Este é o primeiro contraste entre a operação tradicional e a operação melhorada através dos conceitos do Sistema Toyota de Produção.
Costurar em alta velocidade é melhor?
Aposto que você conseguiria dizer facilmente as vantagens de costurar em alta velocidade, mas poderia acabar sendo um grande desafio pensar nas vantagens de costurar lentamente. Costurar lentamente seria mais um dos contrastes que encontraríamos nas linhas da The World Company. Lá você conseguiria enxergar a agulha se movendo, quase como se estivesse sendo operada manualmente.
Não é eficiente costurar em altíssimas velocidades. Cada artigo de vestuário deve ser costurado em sequência, de um processo para o outro. Se a máquina costurar muito rápido, você terá um acumulo de peças costuradas por aquela máquina. Além do mais, rodar uma máquina de costura em alta velocidade significa um número maior de defeitos. Uma vez que algo é costurado erroneamente, é impossível refazer. É melhor costurar com uma velocidade menor, mas com menos defeitos. – explica o Sr. Hatasaki
Uma vez que a Qualidade é um dos principais fatores da Produtividade, o Sr. Hatasaki demonstra que é inútil tentar aumentar a Produtividade através da velocidade. Produzir defeitos mais rapidamente não significa ser mais produtivo, pois o tempo economizado será gasto em retrabalho, isso quando possível; fora outros custos que vem com os defeitos.
O que é mais rápido: fazer um carro ou um vestido?
Antes da chegada do NPS, o Lead Time da produção de um vestido na The World Company era de 25 dias. Se acelerassem a produção, entregavam em 20 dias. Mas o produto recebia valor agregado somente durante 1,5 horas destes longos 25 dias.
Leva menos de um dia para se produzir um carro. Por que demora-se dias, até semanas, para se produzir uma jaqueta ou um vestido. É algo que te faz pensar.
Com o método correto, o Sr. Hatasaki sabia que seria possível produzir cada peça em um tempo muito menor. É o conceito básico de que “o tempo é a sombra do movimento”. Tradicionalmente, o que encontramos em uma industria é a busca pela eficiência dos recursos, onde cada equipamento produz centenas, milhares do mesmo produto: primeiro um grande lote de mangas, depois um grande lote de colarinhos, depois um grande lote de bolsos. Isso leva ao efeito dos lotes na eficiência do fluxo, onde produzir uma peça completa leva um tempo enorme, composto em sua maior parte, de espera.
Ao eliminar a superprodução e focar na eficiência do fluxo, a empresa conseguiu reduzir drasticamente o tempo necessário para terminar um vestido. Vamos ver um exemplo imaginário da situação para ficar claro o efeito dos lotes:
Imagine que seu vestido é fabricado em dois processos, A e B. A produz a parte superior e B costura a parte superior na parte inferior do vestido (já percebeu que eu não entendo nada de componentes de roupa, não?) e você trabalha em lotes: primeiro produz 10 unidades de parte superior no processo A, e só então envia para o processo B. Cada processo demora 1 minuto. Quanto tempo você demora, neste cenário, para ter a primeira unidade de vestido pronto?
Desconsiderando tempos de transporte, e considerando que o processo B tem que esperar o processo A produzir 10 unidades de parte superior antes de receber trabalho, são 10 x 1 minuto, mais o 1 minuto que o processo B leva para executar sua parte do trabalho. Um total de no mínimo 11 minutos para ter a primeira unidade de vestido pronta. Se você também trabalhar em lotes no processo B, fica ainda mais demorado.
Mas seguindo um fluxo contínuo, de “consuma um, produza um”, onde o processo A produz uma unidade da parte superior e já envia para o processo B, teríamos a primeira unidade de vestido pronto em 2 minutos. Isso resulta em uma redução de 72% no Lead Time do primeiro vestido. Se o processo seguir assim, a cada 1 minuto você teria 1 vestido pronto saindo da linha. Isso te torna flexível, adaptável às mudanças de design e na demanda dos clientes. Mesmo que um cliente vá comprar um lote de 10 deste vestido, produzindo um a um você pode interromper a produção com um prejuízo muito menor caso ele altere a quantidade ou caso surja um defeito no processo, do que se já tivesse começado 10 peças. Imagine o efeito dessa flexibilidade diante de uma situação real, com custos de produção reais e lotes de compra grandes.
Um outro fator que tornou essa flexibilidade fundamental para a The World Company é bem característico da industria da moda:
Na industria da moda, devemos evitar a superprodução. […] superprodução geralmente leva a descontos. Quando você começa a dar descontos, a imagem da sua marca sofre. Uma boa imagem da marca é muito importante. Pegue por exemplo, roupas para a prática de golfe. Roupas para este esporte são de altíssima qualidade. Mas elas são produzidas em excesso e precisam de descontos. Agora todos estão vestindo roupas deste tipo […]. Não importa mais se os grandes profissionais estão vestindo. A imagem da roupa foi afetada, e você não poderá mais vendê-la por um preço alto. As pessoas deixam de achar que estão vestindo algo exclusivo.
Após a prática do NPS, a empresa passou a conseguir produzir uma peça de roupa a cada 2h, podendo produzir conforme a chegada de pedidos, eliminando a necessidade de manter estoques de produto acabado.
Terceirizar realmente reduz custos?
Outra lição importante que a The World Company aprendeu com o NPS foi a não terceirizar a produção. Devemos evitar ao máximo essa prática.
Terceirizar envolve um grande trabalho suplementar. Você precisa determinar o quanto pedir. Precisa considerar o transporte, e a emissão de pedidos de compra. Você não tem certeza absoluta de quando os produtos vão chegar. Pode ser que você tenha que buscar os produtos, refazer um pedido e estocar a entrega. É muito trabalho e contém muito desperdício. Geralmente, é muito melhor produzir você mesmo. Temos a tendência de achar que terceirizar reduz custos, mas há custos e desperdícios ocultos.
Um dos efeitos da prática constante do kaizen é a liberação de espaço, pessoas e capacidade produtiva. Um movimento externamente inteligente e menos arriscado do que depender somente de criar novos produtos e se meter em mercados desconhecidos é começar a fabricar internamente aquilo que antes era terceirizado, tornando muito mais simples o processo de controlar a qualidade, produtividade e consequentemente, custos. Ainda há a vantagem de poder se tornar fornecedor dos seus concorrentes que não tem essa capacidade de aprendizado e kaizen.
Kaizen e prosperidade
O resultado destes contrastes e inúmeros outros gerou muita prosperidade para o negócio. Mesmo em uma industria de lucros instáveis, a The World Company conseguiu, em 1984, um lucro de $563 milhões de dólares, enquanto o lucro de suas concorrentes da época, Onward, Renown e Wacoal permaneceu em torno de 43 milhões de dólares. Se somadas as subsidiarias da empresa, o lucro foi ainda maior, totalizando $823 milhões.
Um importante lembrete é que esse lucro deve retornar também para os operadores e colaboradores no geral. Uma empresa que lucra cada vez mais com o kaizen e não divide a prosperidade com os principais executores não está operando corretamente, e logo seus esforços de melhoria irão decair. O esquecido princípio do Respeito pelas Pessoas significa que todos devem prosperar com a melhoria. A cultura kaizen não floresce em ambiente de egoísmo e ganha-perde.
No final das contas, uma única coisa não sai de moda
Este foi um pequeno resumo, acompanhado de uma breve análise dos pontos de destaque da grande mudança que aconteceu na The World Company, em especial, na cabeça de seu presidente. Sem a mudança na mente dele, nada disso seria possível. E isso fica claro em sua declaração final:
O que é considerado senso comum frequentemente não passa de hábitos cegos. Por ser feito de tal maneira, você nunca questiona. É fé cega. Você não pode desenvolver algo novo a não ser que questione a prática atual e praticamente sinta que você mesmo deve mudá-la.
A coisa mais importante é ter uma atitude questionadora. Os métodos do NPS foram completamente contra o senso comum. No passado, eu assistiria minhas máquinas cortando metros e mais metros de tecido de uma vez só, e aquilo me faria me sentir bem. Você realmente sente que está trabalhando. Se eu visitasse outras empresas, eu veria os equipamentos mais modernos, e iria querer ter aquilo também.
Mas agora quando eu visito alguma planta e vejo equipamentos dos mais modernos, eu agora sei que aquela planta não é adaptativa. Você pede a eles que produzam em lotes de 10 ou 20. Eles não conseguem, e isso é um ponto muito importante. A era da produção em massa ser sinônimo de baixo custo acabou. O importante agora é produzir no momento certo e somente a quantidade necessária.
É claro, é mais fácil falar do que fazer. Nós éramos inexperientes. Os instrutores do NPS disseram que éramos como crianças no jardim de infância. O que eles querem dizer é que não há fim para a melhoria, há mais coisas a se fazer. Nós agora entendemos que a melhoria criativa e a inovação não tem fim. Não temos a meta audaciosa de antecipar a moda do futuro. Tudo o que estamos tentando fazer é criar uma empresa que seja capaz de responder aos desejos dos clientes.
Espero que essa breve análise e a sabedoria do Sr. Hatasaki sirvam de inspiração para você na sua jornada kaizen. Nunca se esqueça: a única coisa que nunca vai sair de moda é o kaizen!
Um grande abraço e até a próxima.
Comentários